Energy and Climate Protection
As an energy-intensive company, we take responsibility for the efficient use of energy and global climate protection and are committed to the Paris Climate Agreement. The transformation of BASF toward climate neutrality is a challenge. We are determined to follow this path and become a pioneer in low-emission chemistry.
At a glance
16.9 million metric tons
Scope 1 and Scope 2 greenhouse gas emissions1
2.6 TWh
Electricity from renewable energy
- Ambitious emission reduction targets
– Net Zero Accelerator unit promotes measures - New Scope 3.1 target3 to reduce raw materials procurement emissions
– Supplier CO2 Management Program for suppliers - Corporate and product carbon footprints create transparency
Strategy and governance
Our products and solutions contribute to reducing greenhouse gas emissions in many areas. At the same time, we are working to significantly reduce our CO2 emissions2 along the value chain. This creates opportunities for our business activities: Thanks to our transformation toward climate neutrality, we can increasingly offer our customers products with a reduced product carbon footprint (PCF). However, emissions from our production, our energy procurement and our upstream and downstream value chain have a negative impact on the climate. Climate protection is therefore very important to us and is an important part of our corporate strategy. Climate scenarios are incorporated into the strategies of our business units. We continuously analyze short and long-term opportunities and risks for our business operations arising in connection with the topics of energy and climate protection as part of our opportunity and risk management.
We are pursuing ambitious climate protection targets. In addition to the targets for reducing our emissions from production processes (Scope 1)1 and the purchase of energy (Scope 2)1, we set ourselves a target for reducing our specific raw materials-related emissions (Scope 3.1)3 in the reporting year. Based on increased transparency and data availability, we will be able to steer our upstream emissions, which make up the majority of our total emissions along the value chain, in a more targeted manner in the future. We have extended our long-term target of achieving net-zero greenhouse gas emissions by 2050 and are striving toward this target for Scope 3.1 in addition to Scope 1 and 2 (see below).
2030 targets
–25%
Reduction in our absolute Scope 1 and 2 greenhouse gas emissions1 compared with 2018
–15%
Reduction in our specific Scope 3.1 greenhouse gas emissions3 compared with 2022
2050 target
Net-zero
Greenhouse gas emissions by 2050 (Scope 1, 21 and 3.1)
To reduce our greenhouse gas emissions and demand for fossil raw materials, we are focusing on the following measures:
- Renewable energy: We are increasingly meeting our electricity needs from renewable sources (see “Energy supply”).
- CO2 abatement: We are taking targeted measures to avoid CO2 emissions: These include lower-emission steam generation (see “Energy supply”), the development of new technologies (see “Climate-smart technologies”) and continuous measures in the area of operational excellence (see “Energy efficiency”).
- Circularity: We are increasingly using renewable and recycled raw materials as well as raw materials based on the use of CO2 in order to move from linear value creation to closed material cycles (see “Raw materials”).
We only consider external offsetting measures for our Scope 1 and Scope 2 emissions1 as a temporary solution in the medium term if our activities do not make the desired contribution to reducing emissions. We bundle measures to achieve our Scope 3.1 target3 primarily in purchasing-specific measures (see below).
By adjusting our organizational structures, we have created the conditions for implementing our climate protection targets and the measures that contribute to them in a focused and swift manner: The Corporate Center’s Environmental Protection, Health, Safety and Quality (EHSQ) unit, which reports to the Board of Executive Directors, develops Group-wide requirements and guidelines for collecting emissions and energy data and for energy management. It conducts regular audits to monitor the implementation of and compliance with internal guidelines and legal requirements by our sites and Group companies. The Corporate Strategy & Sustainability unit develops the BASF Group’s climate targets and strategic levers for achieving them. The driving force behind the implementation is the Net Zero Accelerator unit, which focuses on the accelerated implementation of existing and new cross-divisional projects to reduce emissions. The Global Procurement unit, together with Corporate Development, is responsible for purchasing processes and procurement guidelines with regard to our raw materials-related targets. Global Procurement reports to the Chief Financial Officer; the Corporate Sustainability and Net Zero Accelerator units report to the Chairman of the Board of Executive Directors. This enables us to lay the foundation for integrating climate protection-relevant aspects into strategic decision-making processes such as investments, acquisitions and core business activities. Group-wide Scope 1 and Scope 2 emissions have been anchored in the BASF Group’s steering and compensation systems as the most important nonfinancial key performance indicator since 2020, giving them even more weight.
By reducing our own CO2 emissions and those upstream in the value chain, we contribute to our customers achieving their climate protection targets. To increase transparency and target our CO2 reduction measures to those areas where they bring the greatest added value, we continuously determine the Product Carbon Footprint for around 45,000 sales products (see “Product Carbon Footprints”). In addition, we offer our customers solutions that help prevent greenhouse gas emissions and improve energy and resource efficiency.
We are committed to reporting transparently on our climate protection targets and progress, as well as on the impact of climate change on BASF. In this context, we support the recommendations of the Task Force on Climate-related Financial Disclosures (TCFD). Since 2019, BASF’s annual report has included an overview showing the sections and subsections in which TCFD-relevant information can be found. We also participate in the program established by the international nonprofit organization CDP for reporting on data relevant to climate protection and have done so since 2004. BASF achieved a score of A– in CDP’s 2023 climate change questionnaire, again attaining Leadership status. Companies at the leadership level are distinguished by factors such as the completeness and transparency of their reporting.
All parts of society must work together to effectively protect the climate. This is why we support various national and international initiatives and are involved in partnerships. For example, we engaged in close dialog with the Science Based Targets initiative (SBTi) to derive science-based climate protection targets for the chemical sector.
1 Excluding the sale of energy to third parties. Greenhouse gases are converted into CO2 equivalents (CO2e) in accordance with the Greenhouse Gas Protocol
2 The term “CO2 emissions” includes all greenhouse gases in accordance with the Greenhouse Gas Protocol and is used synonymously with “greenhouse gas emissions.”
3 Scope 3.1, raw materials excluding battery materials, excluding services and technical goods. Excluding greenhouse gas emissions from BASF trading business. Future adjustment of the baseline in line with the TfS guideline possible depending on the availability of further primary data.
Development of the BASF Group’s greenhouse gas emissions (Scope 1 and 2)4
Million metric tons of CO2 equivalents
Global targets
Compared with the 2018 baseline, we want to reduce greenhouse gas emissions from our production processes (Scope 1) and our energy purchases (Scope 2) by 25% by 2030.4 This means that we aim to reduce greenhouse gas emissions from 21.9 million metric tons to 16.4 million metric tons – despite our growth plans and the construction of a new Verbund site in Southern China. This corresponds to a decrease of around 60% compared with 1990. Our long-term goal is net-zero greenhouse gas emissions by 2050.4
In 2023, the BASF Group’s emissions from production and energy purchases4 amounted to 16.9 million metric tons of CO2 equivalents (2022: 18.4 million metric tons). The decline compared with the previous year as a result of a weak economy led to persistently low production volumes and therefore lower emissions in 2023. The share of electricity from renewable sources was increased compared with the previous year, to 20%, and, together with measures to increase energy and process efficiency, made a relevant contribution to reducing emissions.
4 Scope 1 and Scope 2 (excluding the sale of energy to third parties). The target includes greenhouse gases according to the Greenhouse Gas Protocol, which are converted into CO2 equivalents (CO2e).
We also set ourselves an ambitious Scope 3.1 target5 for our specific raw materials-related emissions in the reporting year. By 2030, we want to reduce these in relation to the purchasing volume specifically by 15% from the 2022 baseline. This does not initially include raw materials-related emissions from battery materials, which we intend to further expand in the coming years. Battery materials make a significant contribution to reducing CO2 emissions and thus facilitate the transformation of the transportation sector. Required raw materials such as lithium, nickel and cobalt will not be able to be replaced by more sustainable alternatives in the foreseeable future. Accordingly, we cannot reduce the associated emissions significantly in the short term. As soon as recyclable solutions come into play with the increase in available end-of-life batteries, we will include these raw materials in our target definition (more information on our battery recycling activities).
In 2023, specific Scope 3.1 emissions5 amounted to 1.61 kilograms of CO2 per kilogram of raw material purchased (2022: 1.586). This increase is attributable to the decline in production and the associated reduced use of raw materials in Europe.
In the long term, we strive to reduce Scope 3.1 emissions to an unavoidable minimum by 2050, thereby expanding our long-term net-zero target to include these greenhouse gas emissions. Despite all our efforts, there will be residual share of emissions in 2050 that cannot be avoided using technical or economic approaches. These emissions must be offset by measurements outside our value chains. One option is to sequester carbon into the soil through farming (carbon farming).
- More information on climate protection
- Our projection of greenhouse gas emissions for 2024 can be found in the forecast
Development of the BASF Group’s greenhouse gas emissions (Scope 3.1)
Energy supply
Our total energy consumption was 50.1 million MWh in 2023 (2022: 52.9 million MWh), slightly below the prior-year figure due to the lower production levels. Total energy consumption includes fuel demand in our own central power and steam generation plants, primary energy requirements in our process plants, and net power and steam imports.
To generate our own steam and power, we mainly use natural gas (78.8%) and substitute fuels (17.8%). The latter are residues from chemical production plants that cannot be reused in the BASF Verbund. In 2023, we covered 51% of our electricity demand with our own gas and steam turbines in highly efficient combined heat and power plants. Combined heat and power generation reduces the carbon footprint of our energy production and ensures that fuels are used as efficiently as possible: For instance, compared with separate methods of generating steam and electricity, we saved 10.8 million MWh of fossil fuels and avoided 2.2 million metric tons of CO2 emissions in 2023.7 To achieve the highest possible energy yield with the lowest possible greenhouse gas emissions, we continuously optimize our combined heat and power plants. In 2023, internally generated power in the BASF Group had a carbon footprint of around 0.26 metric tons of CO2 per MWh of electricity and was below the national grid factor at most BASF sites.
The Verbund system is also key to carbon-optimized energy supply at our sites. It helps us realize synergies and manage value chains in a resource-efficient way. For example, waste heat from one plant’s production process is used as energy in other plants. The Verbund saved us around 17.3 million MWh in 2023, which translates to 3.5 million metric tons less CO2 released into the atmosphere.7 With combined power and steam generation as well as our continuously optimized Energy Verbund, we were thus able to avoid a total of 5.7 million metric tons of CO2 emissions in 2023. We will continue to invest in the creation and optimization of Verbund structures and drive forward the consolidation of production at highly efficient sites.
5 Scope 3.1, raw materials excluding battery materials, excluding services and technical goods, excluding greenhouse gas emissions from BASF trading business. Future adjustment of the baseline in line with the TfS guideline possible depending on the availability of further primary data.
6 The value for 2022 was adjusted due to increased data availability.
7 Calculation basis: electricity conversion efficiency of conventional power plants: 45%; steam generation efficiency 90%
A core component in reducing our greenhouse gas emissions is the gradual conversion of our energy supply from fossil to renewable sources. This mainly affects our electricity supply. In 2023, electricity from renewable sources as a share of total electricity consumption rose compared with the previous year to 20% (2022: 17%8). Our electricity consumption will increase significantly in the coming years due to the planned gradual electrification of our steam generation and the switch from natural gas-based to electricity-based, low-emission production processes, for example in our steam crackers (see below). Nevertheless, we aim to source more than 60% of our power needs from renewable sources by 2030.
In the transformation of our power supply, we are pursuing a make & buy approach. Firstly, BASF is investing in its own renewable power assets. Secondly, we are purchasing green power on the market through long-term supply agreements with plant operators, power purchase agreements or renewable energy certificates, depending on the region and market regulations. Profitability and additionality are key purchasing criteria: This means that the electricity purchased is primarily sourced from new renewable energy facilities.
In 2023, we successfully advanced our plan for a power supply from renewable sources. The Hollandse Kust Zuid offshore wind farm, a joint project with Vattenfall and Allianz, was officially inaugurated in fall 2023 and should be fully operational in 2024. With 139 turbines and a capacity of 1.5 gigawatts, it is one of the largest offshore wind farms in the world. We have signed a memorandum of understanding with Vattenfall for a shareholding in the wind farms Nordlicht 1 and 2 as part of a further project. It is envisaged that 49% of the shares will be sold to BASF. Construction is due to start in 2026, subject the final investment decision, expected in 2025. With a total capacity of 1.6 gigawatts, the wind farm should be completely operational in 2028. We plan to use just under half of the electricity generated to supply our production sites in Europe, particularly Ludwigshafen, Germany. In order to be able to fully supply our Verbund site in Zhanjiang in Southern China, which is currently under construction, with electricity from renewable sources in the future, we have entered into a joint venture with Mingyang for an offshore wind farm in Southern China, which includes development, construction and operation. The planned wind farm in Zhanjiang in the province of Guangdong will have a capacity of 500 megawatts and is scheduled to go into operation in 2025, subject to approval. We have also extended our long-term supply contract with the State Power Investment Corporation (SPIC) and secured a supply of 1,000 gigawatt hours of green electricity per year from 2025. In 2023, we also concluded further long-term supply agreements for green power at other sites in Asia, such as the Verbund site in Nanjing, China, and our sites in South Korea. In North America, for example, we were able to secure around 250 megawatts of solar generation capacity through virtual power purchase agreements in 2022. Further long-term supply contracts exist with X-ELIO, providing capacity of 48 megawatts of solar power to supply the Freeport, Texas, site and with EDF Energy Services, providing 35 megawatts of wind energy for the Freeport and Pasadena sites in Texas. In some regions, we have also acquired green power certificates. The aim is to gradually replace these temporary measures with our own power assets or long-term supply agreements.
The carbon footprint of purchased electricity in 2023 was around 0.22 metric tons of CO2 per MWh (market-based approach), slightly below the prior-year level (2022: 0.23 metric tons CO2 per MWh).8
In 2023, we built a stationary long-term sodium sulfur-based storage system (NAS®) at our Schwarzheide site in Germany. It supports the power supply of individual systems via the plant’s own solar park. Together with NGK Insulators Ltd., BASF Stationary Energy Storage GmbH makes NAS batteries and develops them further.
Alongside electricity, steam generation is an important component of our energy supply. In the future, new technologies should make a significant contribution to reducing CO2, for example by recovering energy from the waste heat of our production and infrastructure facilities. In this context, we are examining various concepts such as using electric heat pumps and e-boilers as well as electrifying steam drives.
8 The comparative figure for 2022 has been adjusted to reflect updated data.
Energy supply of the BASF Group 2023 – electricity supplya
Energy supply of the BASF Group 2023 – steam supply
Fossil fuels and residual fuels used in the BASF Group’s central power and steam generation plants
78.8 %
Natural gas
25.3 million MWh
0.9 %
Heating oil
0.3 million MWh
2.5 %
Coal
0.8 million MWh
17.8 %
Substitute fuels
5.7 million MWh
Total:
32.1 million MWh
Good to know
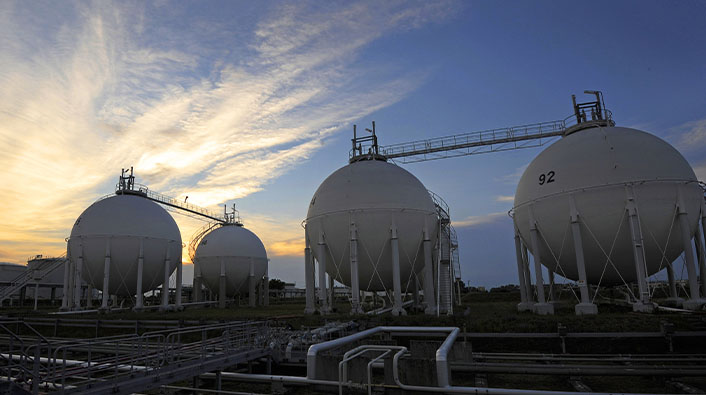
Managing our emissions in the value chain
Reducing Scope 3 emissions presents us with particular challenges, as these are only partly within our own direct sphere of influence and are subject to a large number of external factors. In recent years, we have been able to considerably increase the data availability and thereby transparency of our Scope 3.1 emissions. With our new target and dedicated measures, we want to control upstream emissions in a more targeted manner in the future.
We launched the Supplier CO2 Management Program in 2021 to achieve transparency regarding these emissions. The goal is to obtain a more accurate data base and better manage and reduce emissions in the supply chain. In a first step, we have requested the Product Carbon Footprints of our raw materials since 2021 and support our suppliers in determining these, for example, by sharing our knowledge of valuation and calculation methods with them. Since the start of the program, we have asked more than 1,600 suppliers, covering around 70% of our raw materials-related greenhouse gas emissions. After around two years, we have more than 800 validated Product Carbon Footprints for our raw materials. In a second step, we will now work with our suppliers on solutions to reduce product-related emissions. To this end, we are building up a team of experts in our procurement organization, supported by interdisciplinary experts from the operating divisions and the Net Zero Accelerator unit.
We are also further developing our purchasing processes and establishing the Product Carbon Footprint as a relevant criterion for raw materials in the purchasing guidelines. In addition to reducing our raw materials-related emissions (Scope 3.1), we are taking targeted measures to reduce Scope 3 emissions along the entire value chain. In order to reduce emissions from the use of sold products (Scope 3.11), for example, we rely on product adaptations: For example, climate-damaging blowing agents for foaming polyurethane foams can now be largely dispensed with in the downstream value chain. We also want to reduce emissions resulting from the disposal of our products (Scope 3.12). This is possible, for example, through the increased use of renewable raw materials or circular solutions. Both ensure that less and less CO2 pollutes the atmosphere throughout the life cycle of our products.
Climate-smart technologies
To further reduce CO2 emissions, we are also developing completely new technologies for emission-free and low-emission production. They will need large volumes of electricity from renewable sources in order to realize their full potential. The main focus here is on basic chemicals, which are often still emissions-intensive to produce. This applies, for example, to steam crackers, which use high levels of energy to break down crude petroleum into olefins and aromatics. We made significant progress here in 2023 with the construction of a demonstration plant for electrically heated steam cracker furnaces (see below). Another important basic material in the chemical industry is hydrogen, which we have so far mainly used as a raw material. One common but emissions-intensive way of obtaining hydrogen is steam reforming. We are already testing an alternative process – methane pyrolysis – in Ludwigshafen, Germany. This process is virtually emission-free if renewable energy is used and requires considerably less electricity compared with other methods, such as water electrolysis. We successfully tested a new reactor concept at the pilot plant, which went into operation in 2021, thus overcoming the first important technical hurdle for further scaling. Furthermore, we started construction of a PEM (proton exchange membrane) water electrolyzer9 with a capacity of 54 megawatts at the Ludwigshafen site in Germany with Siemens Energy in 2023. Powered by electricity from renewable energy, the plant, which will go into operation in 2025, is expected to produce up to 8,000 metric tons of emission-free hydrogen and thus reduce greenhouse gas emissions at the site by up to 72,000 metric tons per year. BASF will primarily use the hydrogen produced as a raw material for the manufacture of products with a reduced carbon footprint. In addition, we expect new hydrogen applications in the future, such as energy use, and thus a trend toward increasing demand for hydrogen. Access to large quantities of low-emission or emission-free hydrogen at competitive prices is therefore becoming increasingly important for BASF.
Another focus area of our technological development is carbon capture and storage (CCS). For example, we are currently part of an industrial CCS project at the Antwerp site in Belgium (Kairos@C) as the first phase of the Antwerp@C project, which could enable BASF to avoid the emission of up to 1 million metric tons of CO2 into the atmosphere every year from production. Together with Yara, we are also evaluating the development and construction of a world-scale production plant for low-emission blue ammonia using CCS in the United States. Approximately 95% of the CO2 generated from the production process is to be captured and permanently stored in the ground.
9 The project is funded by the BMWK and the Federal State of Rhineland-Palatinate.
Case study
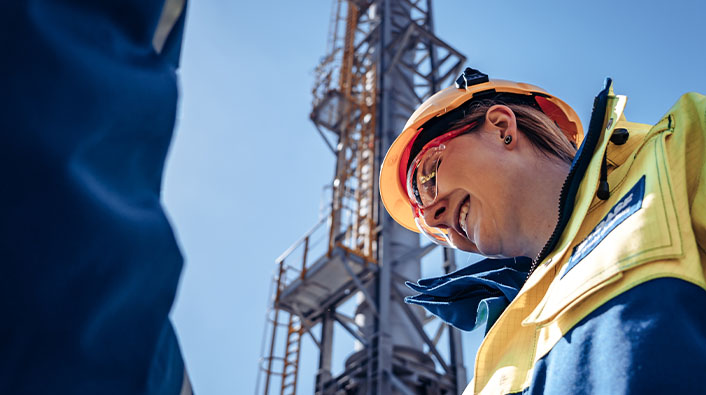
Electrification of our steam crackers
Many everyday products would not exist without steam crackers. They split petroleum into olefins and aromatics – both important groups of substances for numerous chemical value chains. The cracking reaction requires high temperatures of around 850 degrees Celsius, which until now have been achieved by burning natural gas.
Heating concepts that use electricity from renewable sources could reduce process-related emissions by at least 90% in the future. We want to test the feasibility of this new process, as well as direct and indirect heating concepts together with our partners SABIC and Linde in a demonstration plant.10 At the beginning of 2024 this plant was completed at our Ludwigshafen site in Germany and has since then been gradually being put into operation. The prototype is completely integrated into one of the two existing steam crackers at the site.
10 The project has been granted €14.8 million from Germany’s Federal Ministry for Economic Affairs and Climate Action (BMWK) under the Decarbonization in Industry funding program. This project is also being financed by the European Union via the NextGenerationEU fund.
Energy efficiency and specific greenhouse gas emissions
Energy use and greenhouse gas emissions are closely linked to capacity utilization at our plants and its product portfolio. Specific greenhouse gas emissions in 2023 amounted to 0.584 metric tons of CO2 equivalents per metric ton of sales product,11 an increase of 1.2% compared with the previous year (2022: 0.577 metric tons). This was mainly due to persistently lower and inconsistent capacity utilization at our plants, which resulted in a decline in plant efficiency. In contrast, the use of renewable power had a positive impact on specific greenhouse gas emissions. Since 1990, we have been able to lower our overall greenhouse gas emissions from BASF operations by 57.8% and even reduce specific emissions (per metric ton of sales product) by 74.5%.
Through our operational excellence projects, we aim to make our plants and processes even more efficient and resource saving, thereby avoiding CO2 emissions. Certified energy management systems according to DIN EN ISO 50001 at all relevant production sites12 play a particularly important role here. These help us to identify and implement further potential for improvement in energy efficiency. This not only reduces greenhouse gas emissions and saves valuable energy resources but also increases our competitiveness. In 2023, 78 production sites worldwide had certified energy management systems, representing around 89% of our primary energy demand.
A global working group provides ongoing support to the sites and Group companies in implementing and maintaining certified energy management systems. All energy efficiency measures are recorded in a global database, analyzed and made available to BASF sites as examples of best practices.
In 2023, we implemented more than 500 measures to reduce energy and resource consumption and increase our competitiveness. In our steam cracker in Ludwigshafen, Germany, for example, we were able to monitor and analyze energy consumption more specifically by introducing a digital tool for energy optimization, thereby further optimizing the energy efficiency of the crude gas compression process and cracking furnaces. This enables us to avoid more than 15,000 metric tons of CO2 emissions per year. At a plant in Freeport, Texas, an optimized control system increased process efficiency while reducing the power consumption of the compressors. This led to an annual reduction of more than 6,000 metric tons of CO2. In Caojing, China, we can reduce annual emissions by more than 25,000 metric tons of CO2 by harnessing reaction heat through process adjustments and the integration of an absorption heat pump for steam generation.
11 Sales product volumes include sales between BASF Group companies; merchandise is not taken into account.
12 Relevant sites are selected based on the amount of primary energy used and local energy prices.
Corporate carbon footprint
BASF has published a comprehensive corporate carbon footprint every year since 2008. This reports on all emissions along the value chain – from raw materials extraction to production and disposal. We are continually working to reduce greenhouse gas emissions both in our own production and, together with our partners, along the value chain (see “Strategy and governance”).
|
2023 |
2022 |
2018 (baseline) |
|||||||||||
---|---|---|---|---|---|---|---|---|---|---|---|---|---|---|
Specific greenhouse gas emissionsa (metric tons of CO2 equivalents per metric ton of sales productb) |
0.584 |
0.577 |
0.577 |
|||||||||||
Primary energy demandc (million MWh) |
49.917 |
54.206 |
60.586 |
|||||||||||
Energy efficiency (kilograms of sales productb per MWh) |
580 |
589 |
626 |
|||||||||||
|
In 2023, our greenhouse gas emissions according to the Greenhouse Gas Protocol, including Scope 1 and Scope 2 emissions13 were 17.851 million metric tons of CO2 equivalents (2022: 19.149 million metric tons14). Of this amount, 87% were Scope 1 emissions (2022: 87%14) and 13% were Scope 2 emissions (2022: 13%14). Carbon dioxide was by far the largest component and accounted for 98% of emissions (2022: 98%).
Scope 3 emissions arising upstream and downstream of our operations in the value chain are calculated in accordance with the Corporate Value Chain (Scope 3) Accounting and Reporting Standard published by the Greenhouse Gas Protocol and the WBCSD Guidance for Accounting and Reporting Corporate GHG Emissions in the Chemical Sector Value Chain (WBCSD Chemicals). For 2023, we calculated Scope 3 emissions of around 85 million metric tons of CO2 equivalents (2022: 94 million metric tons14).15 There was a further reduction in total emissions along the BASF value chain in 2023 due to lower production volumes.
The largest contribution to emissions along the value chain in 2023 was in category 3.1 (purchased raw materials and technical goods and services) at 47 million metric tons of CO2 equivalents (2022: 53 million metric tons14). To calculate these upstream greenhouse gas emissions, we used both primary data from our suppliers from the Supplier CO2 Management Program (see box on “Managing our emissions in the value chain”) and industrial averages and values from external databases.16 We have been able to reduce our emissions from the use of products sold (Scope 3.11) by around 75% since 2018.17 In addition to raw materials-related emissions, the disposal of our products (Scope 3.12) accounts for the second-largest share of our Scope 3 emissions at around 24 million metric tons of CO2 equivalents (2022: 26 million metric tons).
Scope 3 emissions along the BASF value chain in 2023a
Million metric tons of CO2 equivalents
13 Market-based approach, including sale of energy to third parties
14 The comparative figure for 2022 has been adjusted to reflect updated data.
15 In 2023, we changed the calculation of Scope 3 emissions in categories 3.1 and 3.12 due to increased availability of primary and secondary data. This did not lead to any significant changes in the results. For more information on the calculation method, see basf.com/corporate_carbon_footprint
16 The database values are updated on an annual basis. Significant changes in these values are reflected accordingly in our calculations. BASF operations excluding oil and gas business
17 BASF business without oil and gas operations
Product Carbon Footprints
In 2020, we developed a digital solution to make our product-specific greenhouse gas emissions more transparent and thereby determined the carbon footprints of around 45,000 sales products. These Product Carbon Footprints (PCFs) include all greenhouse gas emissions – from raw materials extraction to the finished product leaving the factory gates (“cradle-to-gate”). PCFs provide us with important information for assessing the climate impact of our products and guidance for implementing mitigation measures so that our customers can benefit from reduced CO2 emissions in the value chain.
In 2023, we further expanded our portfolio of products with a certified reduced carbon footprint, including engineering plastics. We already offer some of our products, such as the intermediates neopentyl glycol and propionic acid, the isocyanates MDI and Lupranat®, the amino resin Kaurit® and the adhesive raw material acResin® with a net-zero carbon footprint. These lower PCFs are primarily made possible by the substitution of fossil raw materials. For instance, we use electricity from renewable sources instead of electricity from fossil fuels to produce low-PCF and zero-PCF products. We also use – in whole or in part – renewable, waste-based or recycled raw materials such as castor oil, biomethane or pyrolysis oil from plastic waste. These alternative resources often have a better carbon footprint compared with fossil raw materials. The alternative resources are allocated to the end product using the mass balance approach.
The digital methodology we have developed to calculate PCFs meets general life cycle analysis standards such as ISO 14040, ISO 14044 and ISO 14067, as well as the Greenhouse Gas Protocol Product Standard. In 2023, we received certification from TÜV Rheinland, which confirms that our calculation method and reporting fully comply with the requirements of Together for Sustainability (TfS). We make our automated PCF calculation approach available to interested industry players through partnerships. At the same time, we are involved in various initiatives to drive transparency, harmonization and standardization across the industry. This also took place as part of TfS, where we were involved in the creation of a uniform guideline for calculating the carbon footprint of products in the chemical industry. This will enable the climate impact of products to be directly compared and evaluated based on a standardized approach. A digital solution for sharing PCF data between companies is currently in the pilot phase and should be implemented in 2024.
Harmonizing the approaches used to calculate PCFs allows us to better manage greenhouse gas emissions that arise during the extraction of raw materials or the manufacture of precursors.
BASF operations |
2023 |
2022 |
2018 (baseline) |
|||||||||||||||||
---|---|---|---|---|---|---|---|---|---|---|---|---|---|---|---|---|---|---|---|---|
Scope 1b |
|
|
|
|||||||||||||||||
CO2 (carbon dioxide) |
14.345 |
15.434 |
17.025 |
|||||||||||||||||
N2O (nitrous oxide) |
0.239 |
0.348c |
0.677 |
|||||||||||||||||
CH4 (methane) |
0.025 |
0.025 |
0.027 |
|||||||||||||||||
HFC (hydrofluorocarbons) |
0.026 |
0.035c |
0.091 |
|||||||||||||||||
SF6 (sulfur hexafluoride) |
0 |
0.001 |
0 |
|||||||||||||||||
Scope 2d |
|
|
|
|||||||||||||||||
CO2 |
2.289 |
2.547c |
4.067 |
|||||||||||||||||
Total |
16.924 |
18.390c |
21.887 |
|||||||||||||||||
Offsetting |
0 |
0 |
0 |
|||||||||||||||||
Total after offsetting |
16.924 |
18.390c |
21.887 |
|||||||||||||||||
Sale of energy to third parties (Scope 1)e |
|
|
|
|||||||||||||||||
CO2 |
0.927 |
0.759 |
0.773 |
|||||||||||||||||
Total |
17.851 |
19.149c |
22.660 |
|||||||||||||||||
Use of biomassf |
|
|
|
|||||||||||||||||
CO2 |
0.112 |
0.084 |
n. a. |
|||||||||||||||||
|