In September 2023, around 100 Emergency Response personnel trained for emergencies as part of the major incident drill that takes place twice a year in Ludwigshafen, Germany. The scenario: A defective seal causes a solvent-containing liquid to escape from a system, leading to ignition and deflagration. Exercises of this kind are an integral part of the preventive safety concept at our sites.
Process safety is a core part of safe, reliable and thus future-proof production. Our comprehensive safety concepts are designed to provide the best possible protection for employees, contractors and our sites’ neighbors, and to prevent damage to property and the environment.
Strategy and governance
We rely on comprehensive preventive measures to ensure process safety and are continually improving the safety of our production processes. Opportunities arise in particular in the automation and digitalization of processes. In our complex production plants, incidents may nevertheless occur that have a potential impact on humans and the environment. We systematically record opportunities and risks in the area of process safety as part of our general opportunity and risk management.
2030 targeta
≤ 0.10
Reduce our worldwide High Severity Process Safety Incidents per 200,000 working hoursb
a In 2023, we adjusted our safety targets.
b Hours worked by BASF employees, temporary workers and contractors
For us, emergency response means being prepared at all times and at all locations for a possible incident.
Our production plants are at the heart of our business. To ensure efficient and safe production and to counteract incidents in our plants, we set binding global standards for process safety. Our sites and Group companies are responsible for implementing and complying with Group-wide requirements and local standards. The Environmental Protection, Health, Safety and Quality (EHSQ) unit in the Corporate Center performs regular audits to check compliance with these requirements.
We pursue ambitious targets for process safety. As part of our continuous improvement process, we regularly monitor progress toward our goals. We critically reviewed our occupational and process safety targets and key performance indicators in 2022. Since 2023, we have been focusing on high-severity incidents. Our reporting continues to be based on established industry standards, with a stronger focus on people.
Global targets and measures
We set high safety standards in the planning, construction and operation of our plants around the world. These meet and, in some cases, go beyond local legal requirements. Our global requirements provide the framework for the safe construction and operation of our plants as well as the protection of people and the environment. Our experts develop a safety concept for every plant that considers the key aspects of safety, health and environmental protection – from plant design to the end of production – and that defines respective safety measures.
In order to maintain a high level of safety at our plants worldwide over their entire life cycles, we carry out implementation checks in all our plants at regular intervals based on risk potential to verify the implementation of our safety concepts. This also applies to the timely completion of the prescribed (process) safety assessments and the resulting safety measures. We regularly update our plants’ safety concepts, taking into particular account new findings, technological opportunities and regulatory developments.
We use the number of High Severity Process Safety Incidents (hsPSI) per 200,000 working hours as a reporting indicator. We have set ourselves the target of reducing High Severity Process Safety Incidents to a rate of no more than 0.10 per 200,000 working hours by 2030.2 In 2023, we recorded 0.05 hsPSI per 200,000 working hours worldwide. The rate of all process safety incidents in the BASF Group was 0.3 in 2023 (2022: 0.3). We investigate every incident in detail, analyze causes and use the findings to derive suitable measures. We share the findings in our global network in the interest of continuous improvement.
To reduce process safety incidents, we focus in particular on technical measures, digital solutions and on a leadership culture that places even greater emphasis on process safety and dealing openly with mistakes. In addition, we are continually refining and expanding our training methods and offerings to increase risk awareness and strengthen our safety culture. In 2023, for example, a program to reduce process incidents at our site in Pudong, China, focused on the topic of tightness and the prevention of leaks and covered this in training courses.
We focus our targets on high-severity incidents in order to focus more strongly on people.
We play an active role in improving process safety around the world in internal and external networks, through our involvement in organizations such as the International Council of Chemical Associations (ICCA), the European Process Safety Centre (EPSC) and the Center for Chemical Process Safety (CCPS), and by fostering dialog with government institutions.
2 Hours worked by BASF employees, temporary workers and contractors
Case study
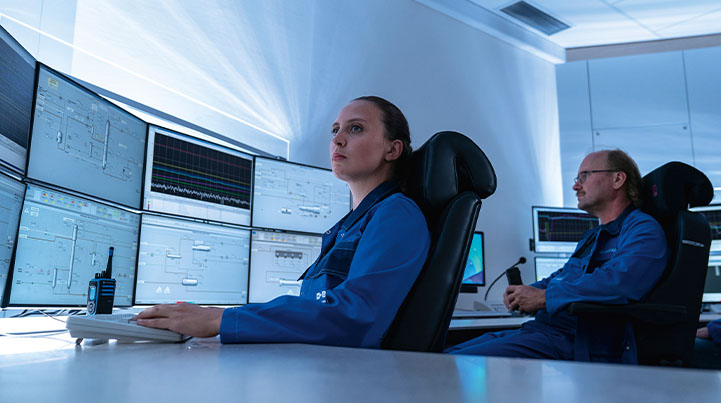
Learning through simulation
An Operator Training Simulator (OTS) can be used to provide a realistic training environment for plant operators so they can learn the skills needed in practice. Similar to a flight simulator, OTS systems can be used to simulate the processes of complex chemical plants.
In this way, new employees can familiarize themselves with their field of work in a practical manner. They can train how to operate the plant, which valves need to be opened or closed under which conditions and which trends in the process control system are particularly important to keep an eye on. An OTS can also be used to simulate conditions that rarely occur in day-to-day work – such as exceptional malfunctions. The simulator is therefore also suitable for training experienced employees.
By using OTSs, we want to further increase the operational safety of our plants and rectify faults faster and better. Several of our operating divisions use simulators. The Petrochemicals division is currently developing OTSs for all of its plant clusters at the Verbund site under construction in Zhanjiang, China, in close cooperation with the Global Engineering Services unit. The advantage of considering an OTS at the same time as planning new projects is that weak points can be identified and rectified before construction begins.
In Nanjing, China; Port Arthur, Texas; Ludwigshafen, Germany; and Antwerp, Belgium, the simulators have already been in successful use at selected plants for several years.