At the beginning of 2024, Zara launched a jacket that is made entirely from recycled polyamide, from the fabric and lining to the hook-and-loop fastener and zipper. Thanks to BASF’s loopamid® solution, the garment is not only made from 100% recycled textile waste, it is also 100% recyclable.
As the world’s population grows, so does demand for limited natural resources. At the same time, many recyclable materials end up in landfill or in waste incineration. Using resources responsibly and closing loops are crucial for our business and achieving our climate targets.
At BASF we think of circularity in two dimensions: In order to achieve our climate targets, we have to not only further reduce our own carbon footprint, but also that of our products. To do this, we use renewable raw materials and recycled raw material sources. At the same time, we are developing products and technologies to help our customers close loops, create value for society and protect the environment.
BASF’s Verbund structure presents numerous opportunities for a circular economy: By intelligently networking our plants, we can use by-products from one plant elsewhere as feedstocks or an energy source, thereby using resources efficiently (see Energy and Climate Protection and In Focus: Emissions to Air, Waste and Remediation). We are also focusing our raw material base even more strongly on nonfossil circular alternatives. We procure these raw materials responsibly in order to minimize negative environmental impacts (for example, biodiversity loss) (see In Focus: Biodiversity and Ecosystems).
Currently, less than 10% of the approximately 350 million metric tons1 of plastic waste generated worldwide each year is currently recycled, yet the global demand for circular feedstocks is rising. The plastics in our product portfolio are mainly used in durable and demanding applications, such as automotive engineering and insulation foams. As a responsible player in the value chain, we are working to further improve the sustainable use of plastics throughout the entire life cycle. That’s why we are developing and marketing solutions for improved mechanical recycling. Where this is not possible, we are driving forward the chemical recycling of plastics as a complementary technology to expand our supply base: Plastics are broken down into their building blocks, which can then be used in production as recycled feedstocks. To do this, we are developing suitable recycling processes, often with partners. In a challenging environment with limited availability of alternative raw materials, we still aim to process 250,000 metric tons of recycled and waste-based raw materials, such as pyrolysis oil from mixed plastic waste or end-of-life tires, in our production plants annually from 2025.
At BASF, embracing the circular economy means not just rethinking materials and production processes, but also our role in the value chain.
Many of BASF’s products and technologies are already helping to close loops at many points along the value chain. Together with our customers and other stakeholders, we want to further accelerate the transformation from linear to circular business models. Our target: By 2030, we want to double our sales of solutions for the circular economy to €17 billion (baseline: 2020). As the sustainable properties of our products have been reassessed since 2023 using the updated TripleS method, this target will be adjusted in the course of 2024.
Our BASF solutions for the circular economy include:
- Products based on renewable or recycled raw materials: These include products manufactured in whole or in part from renewable or recycled instead of fossil raw materials. The alternative raw materials are attributed to the end product, partly using what is known as the mass balance approach. This is verified and certified by independent third parties. We use this approach for example for selected ingredients for the automotive, cosmetics, detergent, cleaner and food industries. Other examples are products to which pyrolysis oil from the chemical recycling of plastic waste can be attributed via the mass balance approach (Ccycled® products), or products that contain mechanically recycled raw materials (Mcycled®).
- Products that close material cycles (“close the loop”): These include products that enable and improve the recyclability of valuable resources. Our first focus area here is the value chain for plastics. For example, multilayer packaging produced with our water-based Epotal® adhesives can be easily separated into its individual recyclable materials during recycling, which can then be reused. We have expanded our ecovio® plastic portfolio and now also offer home-compostable food packaging. The second focus is recycling mineral raw materials. For example, we are driving forward innovative technologies and solutions for recovering metals such as lithium, nickel, cobalt and manganese from end-of-life lithium-ion batteries.
- Products that increase the resource efficiency or lifespan of materials (“extend the loop”): These include products that reduce resource consumption and environmental impact along the value chain. One example is Oxsilan®, an innovative thin-film technology for protecting metals from corrosion, for example, before painting. The process not only enables higher productivity with lower material use, but also offers a favorable safety, health and environmental profile compared with conventional phosphating processes. This category also includes products that extend service life and/or reduce maintenance intervals. Tinuvin® light stabilizers are one example of this. They extend the lifespan of products such as agricultural films by providing reliable protection against UV radiation, heat and agrochemicals.
One of the steps we have taken to meet our targets and accelerate the transformation is establishing a company-wide Circular Economy Program. As part of this program, BASF teams are currently developing new approaches within three main action areas and over 50 initiatives: alternative raw materials pathways, innovative material cycles and new business models for the circular economy – which also include digital and service-based concepts. We also cooperate with partners along the value chain and are involved in numerous networks, such as the Ellen MacArthur Foundation, the World Business Council for Sustainable Development, the Global Battery Alliance and the Alliance to End Plastic Waste. In doing so, we want to better understand needs, trends and growth opportunities and contribute to the development of standards.
1 Bruna Alves, Statista (2023). Lifecycle of plastic waste worldwide in 2019 (infographic). Available at: https://www.statista.com/statistics/1357641/plastic-waste-lifecycle-worldwide/
Case study
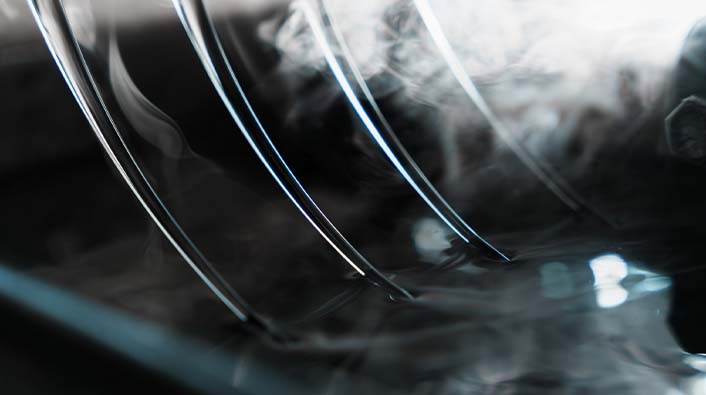
From the clothing bin to the runway
Every year, almost 100 million metric tons of textile waste is produced worldwide, 87% of which is incinerated or disposed of in landfills. At the beginning of 2024, BASF brought an innovative and sustainable solution to the market to boost circularity in the textile industry: loopamid®. Using a new chemical recycling process, textile waste made of polyamide 6 (nylon 6) is first converted into monomers in a process called depolymerization and then purified. The resulting monomers are then converted back into pure polyamide 6 (PA6) through polymerization. This recycled PA6, loopamid®, serves as the raw material for completely new clothing in a circular production model.
BASF is thus offering a solution to close the loop for polyamide 6 in clothing exclusively with textile waste, which can be reused as a valuable feedstock, thereby reducing the consumption of fossil raw materials, for example. loopamid® ensures that textiles remain in their own cycle and garments containing PA6 can be recycled without restrictions. We want to inspire the industry to focus on sustainable textile production and introduce new business models that close loops in textile manufacturing. To this end, we work closely with our partners along the value chain.