Scheduled turnarounds of our production plants harbor risks for work process-related injuries due to nonroutine work and the increased use of contractors. Special initiatives, such as the conduct-based “Consistently safe!” (“Konsequent sicher!”) program at the large-scale turnaround of the styrene plant in Ludwigshafen, Germany, reinforce safety management with holistic approaches to correctly assess risks and establish a common safety culture.
We value the health and safety of people above all else. To ensure safe working conditions we rely on comprehensive preventive measures in occupational safety and health protection. Our comprehensive safety concepts are designed to provide the best possible protection for our employees and contractors.
Strategy and governance
BASF’s long-term economic success is closely linked to the health and well-being as well as the productivity of our employees. In the research and production of chemicals, some of our employees handle hazardous substances and operate complex systems and machines. Potential risks arise as a result, which we aim to minimize through comprehensive preventive measures. We systematically record opportunities and risks in the area of occupational safety and health protection as part of our general opportunity and risk management.
We set binding global standards for occupational safety and health protection. Our health and safety management covers all employees worldwide. Our sites and Group companies are responsible for implementing and complying with Group-wide requirements and local standards. They are supported in this task by global networks of experts. The Environmental Protection, Health, Safety and Quality (EHSQ) unit in the Corporate Center performs regular audits to ensure compliance with the requirements.
2030 targeta
Reduce our worldwide number of High Severity Work Process Related Injuries per 200,000 working hoursb to
≤ 0.05
aIn 2023, we adapted our safety targets.
bHours worked by BASF employees, temporary workers and contractors
The safety and health of all employees who work for us is our top priority – including our contractors.
We pursue ambitious targets for occupational safety as well as for health protection. In the reporting year, we adjusted our occupational safety target and the related reporting based on a Group-wide definition and are now focusing on high-severity injuries (see “Occupational safety”).
We document and analyze accidents as well as their causes and consequences in detail at a global level to learn from them. We consider the systematic hazard assessments and the risk minimization measures derived from them an important prevention tool. With these and a culture of dealing openly with mistakes, division and site-specific safety activities, ongoing qualification measures and dialog across BASF’s global network, we want to strengthen risk awareness among our employees and contractors, share best practice examples and in this way, continually develop our safety culture.
Occupational safety
We have adjusted our targets and reporting based on the critical review of our targets and key performance indicators for occupational safety in 2022. Since 2023, we are focusing on work process-related high-severity injuries. These continue to be based on established industry standards, with a stronger focus on people.
|
Employeesa |
Non-employeesb |
Contractors |
|||||||||||||
---|---|---|---|---|---|---|---|---|---|---|---|---|---|---|---|---|
Fatality ratec |
0.00 |
0.00 |
0.01 |
|||||||||||||
Number of fatalities |
0 |
0 |
2 |
|||||||||||||
Recordable work process-related injury ratec,d |
0.81 |
1.00 |
1.04 |
|||||||||||||
Number of recordable work process-related injuriesd |
788 |
109 |
355 |
|||||||||||||
High-severity work process-related injury ratec |
0.01 |
0.02 |
0.02 |
|||||||||||||
Number of days lost to work process-related injuries and fatalities |
5,262 |
890 |
2,413 |
|||||||||||||
|
We use the number of High Severity Work Process Related Injuries (HSI) per 200,000 working hours as a target. In 2023, we achieved an HSI rate of 0.03. We have set ourselves the goal of reducing high-severity work process-related injuries to a rate of no more than 0.05 HSI per 200,000 working hours by 2030.1 By focusing on high-severity work process-related injuries, we want to make our employees’ working environment even safer.
Despite our efforts, there was one fatal work-related injury in 2023 (2022: 1), in which two people lost their lives. Two contractors suffered fatal injuries in a car accident on a business trip in Brazil. BASF is assisting the authorities in determining the circumstances and cause of the accident.
To prevent work process-related injuries, we encourage and promote risk-conscious behavior and safe working practices, learning from incidents and regular dialog. That is why we are constantly refining and enhancing our global requirements and training.
We encourage and promote risk-conscious and safe working practices.
In addition to the legally required briefings, BASF requires new employees and contractors to complete compulsory health and safety training. Employees at our production sites also receive regular training on the safe handling of chemicals and the correct use of personal protective equipment.
We do everything we can to prevent injuries and use our findings to take appropriate measures to prevent these from happening again, as far as possible. These include regular campaigns and informational events to raise employees’ awareness. Many events and initiatives over the course of 2023 focused on further developing the safety culture, such as a course on the safe handling of forklifts as part of the EHS Culture of Excellence initiative in North America.
Leaders play a key role in the safety culture as role models, which is why environmental protection, health and safety are discussed with newly appointed senior executives. Senior executives with particular responsibility for such topics, for example, in production, also receive specific further training to be able to meet their responsibilities.
To further improve our processes and methods, we evaluate trends in data, analyze accidents and potential incidents, and share knowledge and best practices within our global network of experts and as part of safety initiatives. We also seek dialog with government institutions and are actively involved in external occupational safety initiatives and networks around the world led, for example, by the European Chemical Industry Council (CEFIC) or national associations such as the German Chemical Industry Association and the American Chemistry Council.
1 Hours worked by BASF employees, temporary workers and contractors
Health protection
BASF’s global corporate health management serves to promote and maintain the long-term and holistic health and productivity of our employees. The BASF health checks form the foundation of our global health promotion program and are offered to employees at regular intervals.
We also systematically raise employee awareness of health topics with offerings tailored to specific target groups. One example is the Global Health Campaign. In 2023, we chose a decentralized approach in which the regions and sites could focus on locally relevant health aspects. In North America, for example, the focus was on mindfulness in the professional and private environment. The Take a Moment campaign focused, among other things, on dealing with shift work and mental health. Specific health campaigns were offered at a total of over 459 sites in 2023.
We measure our performance in health protection using the Health Performance Index (HPI). It comprises five components: recognized occupational diseases, medical emergency drills, first aid, preventive medicine and health promotion. Each component contributes a maximum of 0.2 to the total score, meaning that the highest possible score is 1.0. We aim to achieve a value of more than 0.9 every year. With an HPI of 0.96, we once again achieved this in 2023 (2022: 0.96).
In 2023, 44 work-related illnesses among BASF employees worldwide were documented as recognized occupational diseases (2022: 38). The main recognized occupational diseases are occupational asthma, hearing loss, skin diseases, musculoskeletal disorders and cancer.
Another focus in 2023 was on influenza prevention. BASF employees could be vaccinated against seasonal flu at many sites around the world. At the Ludwigshafen site in Germany, for example, around 3,850 employees participated in the influenza vaccination campaign.
Case study
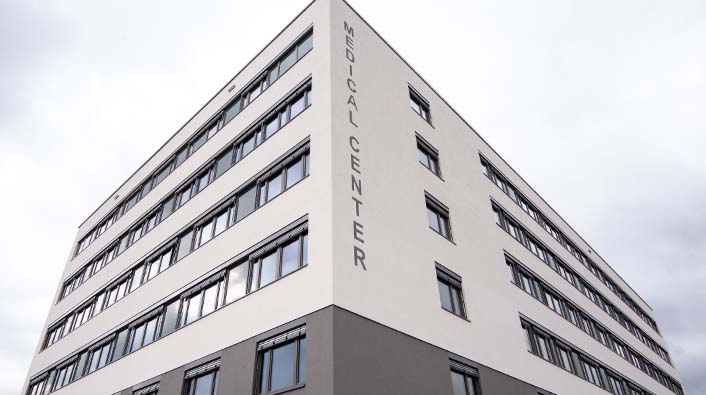
New Medical Center for comprehensive medical care
In 2023, BASF opened a new Medical Center in Ludwigshafen, Germany. The aim is to secure our employees’ health and ensure that they remain able to work despite the rising average age by strengthening medical care at the site in the long term.
Alongside examination and training rooms and offices, it houses state-of-the-art medical diagnostic facilities. In addition to the clinic, the Medical Center accommodates eight external specialist and medical facilities, a physiotherapy practice and a pharmacy. With the exception of the occupational and emergency medicine section reserved for BASF employees, all facilities are also available to our neighbors in the surrounding districts of Ludwigshafen.
Occupational medicine has a long history at BASF: A document from 1866 shows that the first factory doctor was employed at BASF just one year after the company was founded. This also marks the beginning of the first company medical service in the chemical industry in Germany, long before statutory obligations existed.