Energy and climate protection
As an energy-intensive company, we are committed to energy efficiency and global climate protection. We want to reduce emissions along the value chain and utilize, for example, efficient technologies for generating steam and electricity, energy-efficient production processes, and comprehensive energy management. Our climate protection products make an important contribution toward helping our customers avoid emissions.
Strategy
- We are committed to energy efficiency and global climate protection along the value chain
We want to reduce greenhouse gas emissions in our production and along the entire value chain. To this end, we have thoroughly analyzed the greenhouse gas emissions from our production in the past few years and implemented comprehensive reduction measures. This is how, for example, we have been able to significantly reduce nitrous oxide emissions since 1997.
Comparisons with European emissions trading benchmarks show that our greenhouse gas-intensive chemical plants operate at above-average efficiency. To supply our production sites with energy, we rely on highly efficient combined heat and power plants with gas and steam turbines, and on the use of heat released by production processes. Around 50% of BASF Group emissions in 2015 resulted from steam and electricity generation in our power plants as well as in our energy suppliers’ power plants.
Our success also depends on the long-term security and competitiveness of our energy supplies. Furthermore, we are committed to energy management that helps us analyze and continue to improve the energy efficiency of our plants.
We offer our customers solutions that help prevent greenhouse gas emissions and improve energy and resource efficiency. About half of our total annual research spending goes toward the development of these products and the optimization of our processes.
Our climate protection activities are based on comprehensive emissions controlling. We report on greenhouse gas emissions in accordance with the Greenhouse Gas Protocol Standard, as well as the sector-specific standard for the chemical industry. We applied the new Scope 2 standard for the first time in 2015. According to CDP, an international organization that analyzes companies’ climate protection data, BASF is among the top companies in the world in terms of transparency and completeness in climate protection reporting. In reporting to CDP, our experts perform an annual analysis of the opportunities and risks that climate change poses for BASF.
We also advocate economically efficient and environmentally effective climate protection by supporting endeavors to this effect. For example, we joined the U.N.’s Caring for Climate initiative in 2015 – with over 400 companies from 60 countries, this is the largest global business movement in the search for climate change solutions. BASF also advocates the Paris Agreement on climate protection and a global carbon price.
Reduction of greenhouse gas emissions per metric ton of sales product in BASF operations excluding Oil & Gas1,2 (in %)
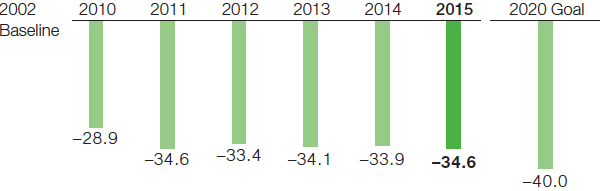
1 The figures for the 2010 and 2011 business years were not adjusted to the scope of consolidation as per the new accounting and reporting standards IFRS 10 and 11. For more information on our data collection methods, see data.
2 The figures for the 2012 business year and earlier were not adjusted to the currently applied factors for global warming potential. For more information on our data collection methods, see this page.
BASF Group’s greenhouse gas emissions according to the Greenhouse Gas Protocol1 |
||||||||||||
BASF operations including Oil & Gas |
|
2002 |
2014 |
2015 |
||||||||
---|---|---|---|---|---|---|---|---|---|---|---|---|
|
||||||||||||
Scope 12 |
|
|
|
|
||||||||
CO2 (carbon dioxide) |
|
14,634 |
16,774 |
16,496 |
||||||||
N2O (nitrous oxide) |
|
6,407 |
669 |
600 |
||||||||
CH4 (methane) |
|
244 |
70 |
88 |
||||||||
HFC (hydrofluorocarbons) |
|
61 |
99 |
119 |
||||||||
SF6 (sulfur hexafluoride) |
|
0 |
0 |
1 |
||||||||
Scope 23 |
|
|
|
|
||||||||
CO2 |
|
5,243 |
3,911 |
3,795 |
||||||||
Total |
|
26,589 |
21,523 |
21,099 |
||||||||
|
|
|
|
|
||||||||
Sale of energy to third parties (Scope 1)4 |
|
|
|
|
||||||||
CO2 |
|
347 |
838 |
1,071 |
||||||||
Total |
|
26,936 |
22,361 |
22,170 |
Global goals
- Specific greenhouse gas emissions reduced
- New goal for energy management system
We aim to reduce our greenhouse gas emissions per metric ton of sales product by 40% by 2020, compared with baseline 2002. In 2015, we achieved a reduction of 34.6% (2014: reduction of 33.9%). Since 1990, we have been able to lower our overall greenhouse gas emissions from BASF operations (excluding Oil & Gas) by 49.8% and even reduce specific emissions by 74.4%.
We set ourselves a new energy efficiency goal in 2015 covering both the chemicals and the oil and gas businesses. By 2020, we want to have introduced certified energy management systems (DIN EN ISO 50001) at all relevant production sites1. Taken together, this represents 90% of BASF’s primary energy demand. This is one of the ways in which we intend to identify and carry out improvements in energy efficiency, reducing not only greenhouse gas emissions and saving valuable energy resources, but also increasing the BASF Group’s competitive ability. In 2015, we were able to complete the ISO 50001 energy management system certification of two additional sites in Germany. This brings the current total to 27 certified sites worldwide, representing 39.5% of our primary energy demand.
1 The selection of relevant sites is determined by the amount of primary energy used and local energy prices.
2020 Goal
–40%
Reduction of greenhouse gas emissions per metric ton of sales product
Baseline 2002
BASF operations excl. Oil & Gas
2020 Goal
90%
Coverage of our primary energy demand by introducing certified energy management systems at all relevant sites
BASF operations incl. Oil & Gas
Introduction of certified energy management systems (ISO 50001) at BASF Group sites worldwide, in terms of primary energy demand (in %)
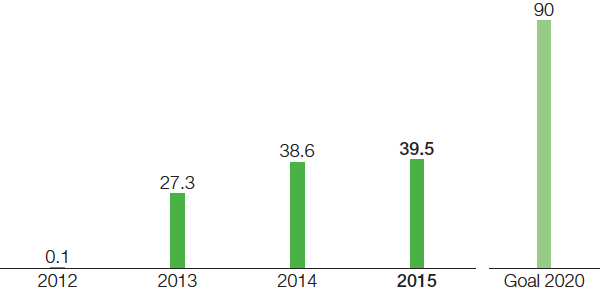
Energy supply of the BASF Group 2015
1 Conversion factor: 0.75 MWh per metric ton of steam
Energy supply and efficiency
- Verbund system as important component of our energy efficiency strategy
Gas and steam turbines in our combined heat and power plants enable us to fulfill around 70% of the electricity demand of the BASF Group. Compared with separate methods of generating steam and electricity, we saved 13.5 million MWh of fossil fuels and prevented 2.7 million metric tons of carbon emissions in 2015. The Verbund system is an important component of our energy efficiency strategy: Waste heat from one plant’s production process is used as energy in other plants. In this way, we saved around 17.6 million MWh in 2015, which corresponds to a savings of 3.5 million metric tons’ worth of carbon emissions. With combined power and steam generation as well as our continuously enhanced Energy Verbund, we were thus able to prevent a total of 6.2 million metric tons of carbon emissions in 2015.
We were able to further optimize the resource and energy consumption of our production in numerous projects around the world in 2015. Various process improvements led to steam and electricity savings. At the Ludwigshafen site, for example, we implemented an integrated steam network between the ethanolamine facility and the Ultrason® plant, making use of significant amounts of heat. The startup of the new, gas-based combined heat and power plant at the Münster site of BASF Coatings additionally supported our endeavors toward efficient and environmentally friendly energy sourcing practices.
We also rely on locally available energy sources for energy supply at our sites. Especially in the growing Asian market, we and our energy suppliers also utilize coal as an energy source since the more climate-friendly natural gas is not available in sufficient quantities at competitive prices.
We are exploring the use of renewable energies. These can only become a permanent part of our energy mix if they are competitive in terms of supply security and cost. Our research also contributes to increasing the efficiency of technologies for the use of renewable energy sources. For example, Deutsche Nanoschicht GmbH – a 100% subsidiary of BASF – has developed an innovative method for producing high-temperature superconductors in a more efficient and environmentally friendly manner. Deutsche Nanoschicht will start operations at a further pilot plant at its Rheinbach, Germany, site in 2016. In cooperation with the Karlsruhe Institute of Technology, high-temperature superconductors are to be optimized for various applications in energy technology.
Key indicators for energy and climate protection in BASF operations excluding Oil & Gas |
||||||||||
|
|
Baseline |
2014 |
2015 |
||||||
---|---|---|---|---|---|---|---|---|---|---|
|
||||||||||
Greenhouse gas emissions2 (million metric tons of CO2 equivalents) |
|
24.713 |
20.550 |
20.133 |
||||||
Specific greenhouse gas emissions (metric tons of CO2 equivalents per ton of sales product) |
|
0.897 |
0.593 |
0.587 |
||||||
Primary energy demand3 (million MWh) |
|
55.759 |
58.962 |
57.262 |
||||||
Energy efficiency (kilograms of sales product per MWh) |
|
494 |
588 |
599 |
Corporate carbon footprint and climate protection products
- Reporting on greenhouse gas emissions along the entire value chain
- Customers’ use of climate protection products sold in 2015 avoids 530 million metric tons of CO2 equivalents
BASF has been publishing a comprehensive corporate carbon footprint since as early as 2008. This reports on all emissions along the value chain and shows the volume of emissions prevented through the use of our climate protection products. We plan our climate protection activities along the value chain based on our corporate carbon footprint.
Through various measures to reduce our raw material and energy requirements, the emission of greenhouse gases associated with producing the raw materials was decreased by a total of around 160,000 metric tons in 2015.
We completed the systematic evaluation of our product portfolio in terms of sustainability considerations in 2015. This included identifying solutions whose application makes a positive contribution in terms of climate protection and energy. Dubbed “Accelerator” products, these are what we focus on when referring to climate protection products. They help us offer solutions to our customers to avoid greenhouse gas emissions over their entire lifecycle as compared with reference products. One example is our Keropur® line of fuel additives, which reduces fuel consumption by optimizing combustion in comparison with conventional fuels.
Greenhouse gas emissions along the BASF value chain in 20151
(in million metric tons of CO2 equivalents)
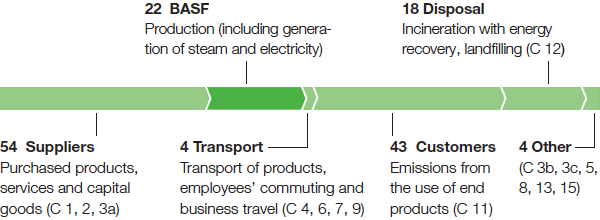
1 According to Greenhouse Gas Protocol, Scope 1, 2 and 3; categories within Scope 3 are shown in parentheses
An analysis of 25 climate protection product groups revealed that customers’ use of products sold in 2015 helped to avoid 530 million metric tons of CO2 equivalents. Every product makes an individual contribution in the value chain of customer solutions. Value chains are assessed in terms of BASF’s economic share of the respective customer solution. On average, 11% of the emissions avoided were attributable to BASF in 2015. The calculation of avoided greenhouse gas emissions was based on the chemical industry standard of the International Council of Chemical Associations (ICCA) and the World Business Council for Sustainable Development (WBCSD).