In Focus: Innovative Processes for Climate-Smart Chemistry
Most of our production processes are already highly optimized. This makes it increasingly difficult to implement further improvements to reduce CO2. Completely new technologies are needed to reduce greenhouse gas emissions over the long term and on a large scale. Different teams are working on this in our Carbon Management R&D Program.
Our focus here is on the production of basic chemicals such as hydrogen. The element is needed as a reaction partner in many processes. The processes currently used to produce hydrogen, such as steam reforming, produce high levels of CO2 emissions. That is why BASF is open to different technologies and is driving forward two alternative processes for climate-smart hydrogen production: water electrolysis and methane pyrolysis. In water electrolysis, water is split directly into its two components, hydrogen and oxygen. If the required energy comes from renewable sources, the process is carbon-free. We intend to use the hydrogen generated by water electrolysis primarily as a material in the BASF Verbund and also, to a limited extent, for hydrogen model region projects in Germany’s Rhine-Neckar region. We are currently working with Siemens Energy on initial concepts for the construction of a PEM (proton exchange membrane) water electrolyzer with a capacity of 50 megawatts at the Ludwigshafen site in Germany. We are also exploring various options for project funding.
In parallel, we are developing methane pyrolysis technology together with partners from academia and industry in a project sponsored by the German Federal Ministry of Education and Research. In this innovative process, (bio)methane is split directly into hydrogen and solid carbon. The process requires around 80% less electricity than water electrolysis and is virtually carbon-free if renewable energy is used. Following extensive groundwork, we started up a test plant for methane pyrolysis at the Ludwigshafen site in Germany in 2021. It will provide insights into the heating concept, as well as the use of new types of materials.
Another focus area is alternative heating concepts for our steam cracker furnaces. We use these plants to split petroleum into olefins and aromatics. This requires temperatures of around 850 degrees Celsius, which are normally achieved by burning fossil fuels – which emits high levels of CO2. A fundamentally new heating concept based on electric resistance heating (eFurnace) and the use of renewable energy could eliminate up to 90% of process-related emissions in the future. To develop and pilot the concept, we signed a cooperation agreement with SABIC and Linde in 2021 and jointly applied for funding to build a demonstration plant.
In addition to new, low-carbon production processes, we are also investigating the use of innovative carbon storage methods. At the Antwerp site in Belgium, BASF plans to invest in one of the largest carbon capture and storage (CCS) projects under the North Sea together with its Antwerp@C consortium partners. The project can potentially avoid more than one million metric tons of CO2 emissions per year from the production of basic chemicals. A final investment decision is targeted for 2022.
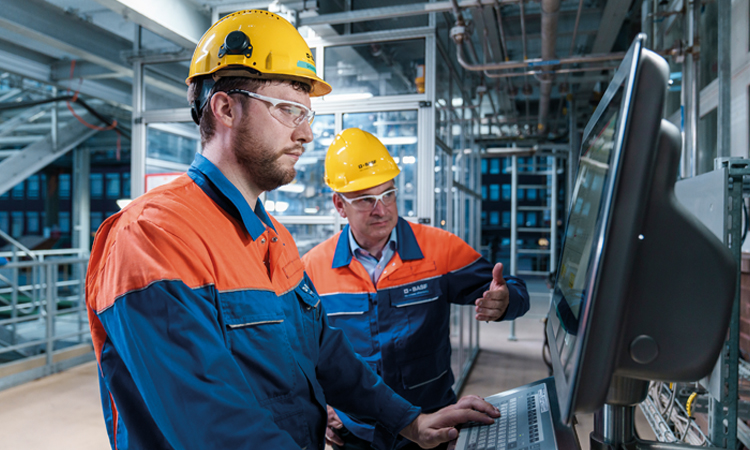