In Focus: BASF Solutions for a Sustainable Future
Solutions based on chemistry are fundamental to a sustainable future. Every day, around 111,000 employees at BASF work to turn good ideas into innovative products that help solve global challenges such as climate change, resource scarcity or food supply.
Enabling climate-smart mobility
The transportation sector is one of the largest sources of greenhouse gases. In Europe, for example, around one-quarter of all CO2 emissions are caused by road traffic. BASF helps to reduce exhaust emissions and vehicle fuel consumption with innovative solutions to treat exhaust gases such as zeolite SCR catalysts or tri-metal catalyst technology, Keropur® fuel additives or lightweight high-performance plastics such as Ultramid®, Ultradur® or Elastoflex®.
At the same time, as a leading supplier of battery materials for lithium-ion batteries, we are paving the way for the age of electromobility. Here, too, the focus is on sustainability – from the responsible procurement of mineral raw materials and the most economical use in production to recycling at the end of the life cycle. In the future, the carbon footprint of our European production will be significantly below the industry standard thanks to our efficient manufacturing processes, the high share of renewable energy, and regional procurement and recycling of key raw materials.
In aviation, the Novaflex Sharkskin surface film developed jointly with Lufthansa Technik leads to noticeable CO2 reductions. Its structure is modeled on sharkskin and optimizes aerodynamics at the flow-related parts of the aircraft. The sharkskin technology will be used on Lufthansa Cargo’s entire freighter fleet from 2022. Through its use on the 10 Boeing 777F freighters alone, Lufthansa Technik expects to save around 3,700 metric tons of kerosene and reduce CO2 by around 11,700 metric tons every year.
Making better use of sun and wind
BASF products enable renewable energies to be used more efficiently. One example is solar salt. This mixture of sodium nitrate and potassium nitrate is used in concentrated solar power (CSP) plants (image below). As a heat transfer fluid at high temperatures of over 550 degrees Celsius, molten solar salt allows solar energy to be stored and thus used even in bad weather or at night.
Other examples are the amine-based hardeners Baxxodur® EC 301 and EC 201. Both have proven effective in processing epoxy resins for the manufacture of rotor blades for modern wind turbines. Baxxodur® hardeners contribute significantly to the advantageous properties of the cured epoxy resin, such as low weight, high mechanical strength, and high chemical and thermal resistance – all of which are key to the longevity of rotor blades.
Avoiding CO2 through efficient thermal insulation
An important lever in reducing CO2 is the energy efficiency of buildings. For a number of years now, we have also offered biomass balance versions of our proven insulating materials Styropor®, Neopor®, Styrodur® and Elastopir®. Under a certified mass balance method, we replace 100% of the fossil raw materials used in the production of these product lines with renewable feedstocks. This significantly reduces the carbon footprint of the end product – in the case of Neopor® BMB, by 66% per cubic meter of insulation panel compared with conventional Neopor®.
Creating new products from waste
Our innovative technologies and solutions help to reduce waste generation and increase the amount of waste that can be recycled. One example is our portfolio of plastics additives. Among other things, these additives help to reduce waste by improving the durability of materials. Additives also enable improved mechanical recycling. For example, the IrgaCycle™ product series launched in 2021 helps our customers avoid certain quality problems in mechanically recycled plastics. This means that recycled plastics can also be used for higher-value applications and recycled content can be increased in the manufacture of new products.
In addition to our mechanical recycling solutions, we are driving forward chemical recycling. In our ChemCycling™ project, our technology partners convert waste such as used tires or mixed plastic waste, which was not previously recycled, into pyrolysis oil. We can feed this pyrolysis oil into our Verbund structure in place of fossil raw materials and use it to make new products based on a certified mass balance approach. This reduces waste, saves resources and simultaneously reduces the carbon footprint of our products. One example is Styropor® Ccycled™, which is used to manufacture products like insulated transport boxes for temperature-sensitive goods such as coronavirus vaccines. Another application is functional textiles. For example, VAUDE will be launching outdoor pants made using our Ultramid® Ccycled™ polyamide from 2022.
Materials such as Infinergy® can be recycled. The expanded polyurethane is used in products such as shoe soles thanks to its outstanding spring and cushioning properties. Through a combination of mechanical processing and finishing, Infinergy can be recycled and regenerated with its original level of material quality.
We also have sustainable solutions for packaging and food containers made of cardboard, such as cups or boxes. Until now, these have typically been coated with a thin layer of polyethylene, which provides a protective barrier to liquids. However, this plastic layer makes recycling difficult. With its Joncryl HPB 4K range, BASF has developed a dispersion system that provides an excellent liquid barrier. Unlike conventional solutions, it is water-based. This makes it possible to efficiently recycle coated cardboard.
Natural ingredients for industrial and consumer goods
Both industrial users and end consumers are increasingly interested in nature-based ingredients. We are addressing this trend with a growing portfolio of plant-based solutions. One example is Disponil® APG 215 for the wood processing industry. Used as an adjuvant in production, this surfactant increases the bond strength of medium-density fiberboard (MDF). This enables manufacturers to achieve a denser and smoother surface and with it, improved water-repellent properties compared with conventional manufacturing processes. Disponil® APG 215 also offers energy saving potential in the production process and is 100% based on natural, renewable plant-based raw materials.
Alongside the natural trend, sensory characteristics such as consistency and texture play an important role in skin and hair care. That is why we are researching and developing alternatives to synthetic ingredients and excipients for cosmetics and personal care products. One example is Hydagen® Clean. Launched on the market in 2021, the biopolymer is characterized by its ease of use and high quality. It can be processed in both cold and hot water and is biodegradable. It is extracted from the tuber of the konjac plant native to southwest China and is suitable for applications such as gels and fluids, as well as novel products such as patches and jelly cosmetics.
Reducing the environmental impacts of agriculture
The demand for food, feed and energy is increasing, while natural resources are limited. Agriculture is a key enabler in providing enough healthy, affordable food. Our innovative solutions help farmers find the right balance between productive and sustainable cultivation. One example is Revysol®. The new fungicidal active ingredient controls several economically important fungal diseases in several key crops globally. Its enhanced efficacy, improved selectivity and favorable regulatory profile allows farmers to maximize yield and to reduce the need to convert more natural habitat to farmland. Revysol®’s performance and its formulation innovation, which provides long-lasting protection under critical weather conditions, avoids the need for repeated fungicide applications. Revysol® helps to significantly reduce CO2 emissions per ton of crop.
BASF tapped the Brazilian market with Pingo Doce™ watermelons, introducing not only high-quality seeds but also a new business model. BASF provides technical support to farmers and demonstrates best practices in efficient water management, fertilization and traceability to establish sustainable production. Regular quality controls are carried out to check the sweetness, color and size of the watermelons in order to reduce the amount of fruit rejected by supermarkets. This new approach delivers a product that benefits farmers, consumers and the environment alike.
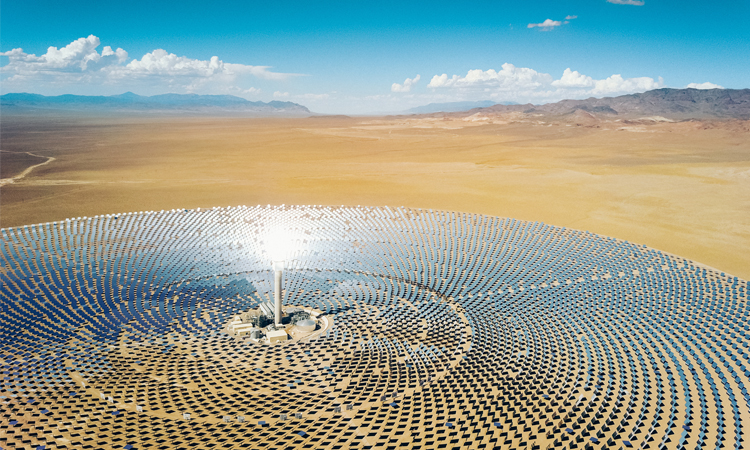