Story
Innovative Processes for Climate-Smart Chemistry
Basic chemicals are the fundamental building blocks of many of our products, enabling our customers to lower their CO2 emissions and make everyday life. The problem, however, is that conventional processes used to produce basic chemicals generate high CO2 emissions, and therefore do not have a long-term perspective, considering BASF’s ambitious climate protection targets. As part of its carbon management program, BASF is developing innovative technologies for the climate-friendly production of basic chemicals such as hydrogen, olefins and aromatic compounds.
Old bricks on the outside and high-tech in the inside. A complex web of pipes, valves and measurement devices. The faint whirring sound in the background makes it difficult to imagine that something groundbreaking is happening here.
Amid all of this, Dieter Flick says: “As we began our research work some 10 years ago, it was not at all foreseeable that this would one day be reality.” Flick is head of methane pyrolysis – besides water electrolysis – one of two BASF projects for the low-carbon production of hydrogen.
The central importance of hydrogen for BASF’s value chains
Hydrogen plays a key role in the chemical industry. The smallest and lightest of all the elements in nature’s toolbox, it is a central and indispensable raw material for important basic chemicals such as ammonia and methanol as well as an integral part of many polymers such as plastics. The current global demand for hydrogen at BASF is about one million tons per year. Of this, about 250,000 tons of hydrogen is produced at the Ludwigshafen site or arises as byproducts in production.
Like every other day, the process engineer is doing his tour of the testing facility, which has been running at the Ludwigshafen site since 2021. Along with his colleague, Florian Schachtschabel, he is checking critical process parameters such as pressure and temperature. “Methane pyrolysis, as an idea, has been around since the 1960s. It hadn’t been implemented till now due to technical difficulties,” says Flick.
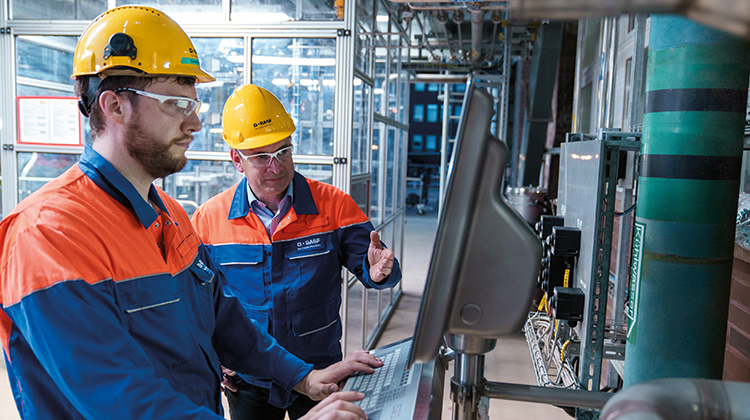
Actually, methane pyrolysis is quite simple in principle: methane (CH4), the main component of natural and biogas, is split directly into its constituent parts carbon (C) and hydrogen (H2) at high temperatures. In comparison with traditional processes for generating hydrogen based on fossil fuels such as steam reforming, hardly any CO2 emissions are produced.
As is so often the case with innovative technologies, the difficulties lie in the detail. “It’s a very long way from the idea to realization with such a project. In addition to researching the pyrolysis process in detail, we also had to test various high-temperature materials and develop a new heating concept, among other things. That can only work with a good team spirit, persistence, expertise from many areas, and an abundance of passion,” says Flick. The project is funded by the Federal Ministry of Education and Research (BMBF).
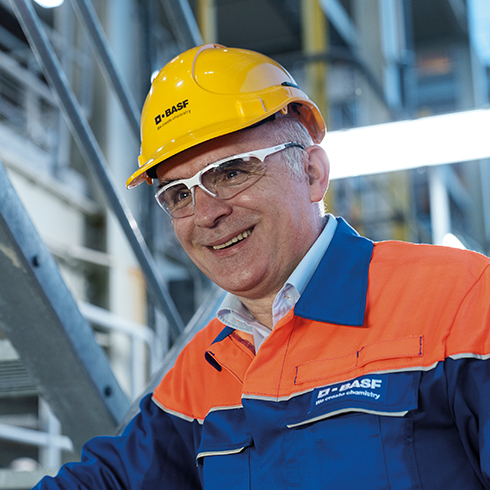
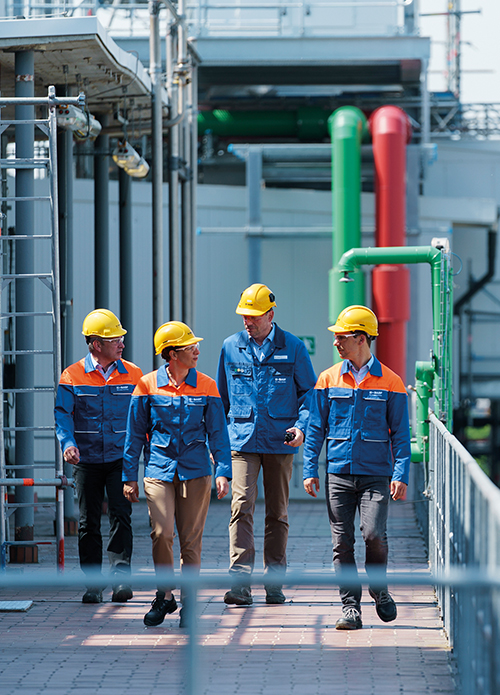
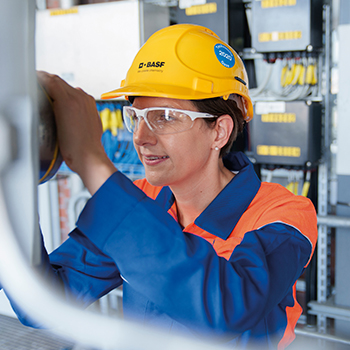
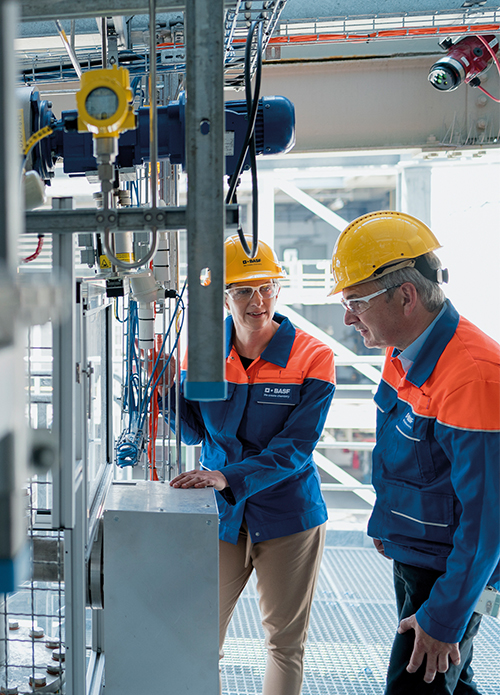
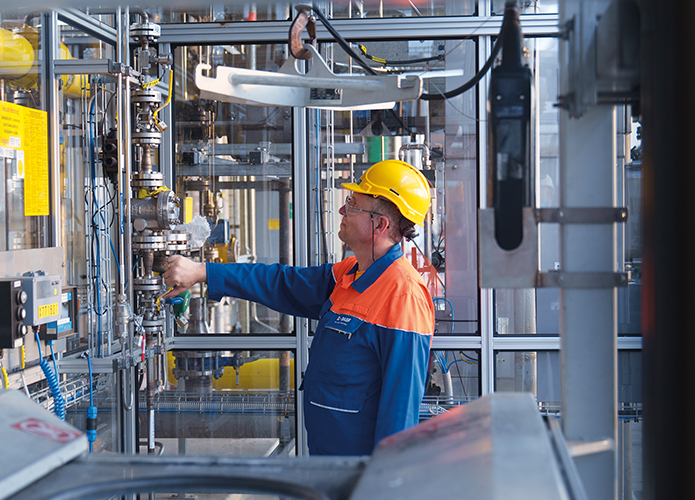
The special feature of the testing facility, which extends over several floors of a BASF technical center, is an innovative reactor concept with the first industrial application of a moving carbon bed worldwide, enabling a high degree of effectiveness and a high level of efficiency. Looking into the future, Flick says, “If the process proves itself in the testing facility, the next steps will be to scale up and construct a pilot plant.”
The methane pyrolysis process
In methane pyrolysis, hydrogen is generated as well as high-purity, solid carbon – a valuable raw material that does not occur naturally. When the testing facility is running stably and there is sufficient carbon, the project team will analyze which applications are technically realizable and useful for the carbon generated by the methane pyrolysis process in the second phase of the project.
Methane pyrolysis for large-scale production should be available by 2030 at the latest. That is an important milestone, as BASF wants to reduce its greenhouse gas emissions by 25% in comparison with 2018 by then. By 2050 BASF wants to achieve net zero emissions from its production sites and its energy purchase. “New CO2-free or low-carbon technologies and production processes are important levers towards these goals,” says Dr. Lukas Mayr, chemist and head of the Carbon Management R&D Program, accelerating numerous projects promoting climate-friendly production of basic chemicals. Being open to different technologies is critical in this process.
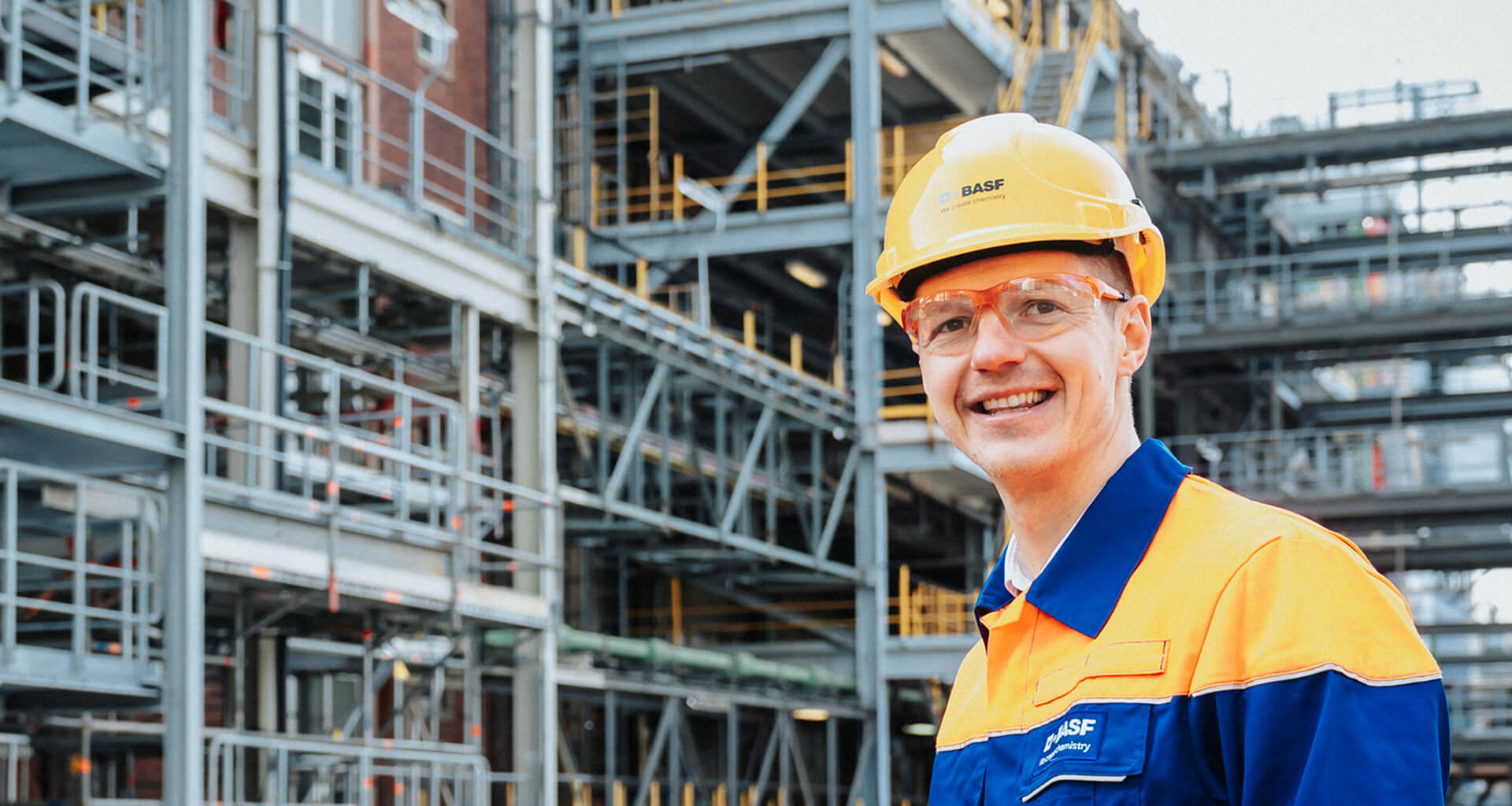
“In the future we will need a mix of different processes and technologies to reach our ambitious climate protection targets,” says Mayr. Besides methane pyrolysis, BASF is also working intensively on water electrolysis for the CO2-free production of hydrogen. In collaboration with Siemens Energy, initial concept planning to build a PEM (proton exchange membrane) electrolyzer at the Ludwigshafen site with a capacity of 50 megawatts is taking place while possibilities for project funding are being investigated.
New opportunities open up for the steam cracker
Alternative heating concepts for steam cracker furnaces are a further example of the transition to climate-friendly production at BASF. In these huge plants, crude oil (naphtha) is split (cracked) into olefins and aromatics – important building blocks for many value chains in the chemical industry – with the help of steam at a temperature of 850°C. Until now, the required temperatures were reached by burning natural gas, leading to high CO2 emissions. BASF wants to break new ground with the eFurnace. “Our approach involves a completely new electric heating system for the steam cracker. This would allow the use of renewable energies, resulting in a reduction of process-related CO2 emissions of up to 90%,” explains Dr. Andrea Haunert, who leads the project in BASF’s Petrochemical division. A joint agreement between BASF, SABIC and Linde was signed in 2021 to develop and pilot the new technology. Together, the partners have applied for funding for the construction of a demonstration plant.
-90%
possible emission reduction by switching to eFurnace
The demand for electricity will significantly increase
Many technical challenges need to be overcome over the next few years before the various innovative processes for a climate-friendly production can be implemented on a large scale. It is also important to realize that nearly all the innovative technologies in the Carbon Management R&D Program avoid CO2 by meeting their energy requirements through the substitution of fossil fuels for energy from renewable resources, particularly green electricity. BASF expects that this switch to climate-neutral production processes will lead to an increase in electricity demand three to four times higher than today alone at the largest production site in Ludwigshafen. The electrification of the steam cracker furnaces, for example, would need the energy generated by 100 large wind turbines. “It is therefore necessary that as much renewable electricity as possible is produced and can be brought to large industrial consumers,” says Dr. Roland Merger, responsible at BASF for projects to supply chemical production with renewable electricity. “If the energy transformation is to succeed, significantly more land must be released for the production of renewable electricity and the electricity grids must be expanded quickly to a significant extent so that there is a sufficient supply of renewable electricity on the market.”
Net Zero Accelerator
The new Net Zero Accelerator unit started work at the beginning of 2022. It bundles all the forces needed to reduce BASF's CO2 emissions by 25% by 2030 and to achieve net zero by 2050. The focus is on three focal points: The first important topic is low-CO2 or CO2-free technologies – “low carbon emission technologies”. These include the methane pyrolysis, for example. The second topic is the supply of renewable energies to our sites, for example through offshore wind farms. Thirdly, there are projects on circular economy, such as our ChemCyclingTM project and renewable raw materials.