Story
A New Lease of Life for Plastics
Humanity is living on credit. The sheer extent of this can be put into figures: In 2021, the credit provided by nature in the form of renewable resources was exhausted after just 210 days. In other words, we would need 1.7 Earths to cover our current global demand for raw materials. The world also has an enormous waste problem. According to a study by the World Bank, the volume of waste generated globally most recently amounted to more than 2 billion metric tons per year – and this value could increase by 70 percent to 3.4 billion metric tons by 2050.
While the causes and negative consequences for the planet are varied, the solution is clear yet also complex: “We need to decouple the consumption of resources and growth from one another,” comments Talke Schaffrannek, who is responsible for circular economy at BASF. This can only be successful with a paradigm shift – away from the currently dominant linear economic model with its “take, use, dispose” approach and toward a system of closed loops with three key principles: reducing the demand for resources and the quantity of waste generated, reusing resources and materials, and returning waste to the circular economy (recycling).
“The chemical industry can take a leading role in this change. Firstly, because the industry itself consumes resources and create waste during production; and secondly, because many of its products and technologies enable the more efficient handling of resources and can close gaps in the circular economy,” says Schaffrannek.
As early as the mid-19th century, BASF founder Friedrich Engelhorn advocated the concept of using waste as raw materials rather than disposing of it. His idea was to produce synthetic dyes from coal tar – a waste product generated during the production of coal gas. He realized at an early stage that it makes economic sense not to solely concentrate on dye manufacturing, but also to integrate the production of the required precursors and intermediates. This was the birth of the Verbund concept in Ludwigshafen, which even today is a characteristic feature of BASF. The intelligent linking and control of plants in a networked Verbund structure enables efficient value chains; for example, by using secondary products from one plant as feedstock elsewhere. This saves raw materials and reduces emissions, as well as lowering logistics costs.
“Thanks to our Verbund concept, the principle of the circular economy and the efficient use of resources have been firmly established at the company for more than 150 years,” states Schaffrannek. In order to strengthen the orientation toward circularity even further, a new, company-wide circular economy program was launched in 2020. This focuses on three fields of action: the increased use of recycled and renewable raw materials, the development of innovative material cycles and the establishment of new business models for the circular economy.
“By 2030, we want to double the sales with solutions for the circular economy to €17 billion. In addition, we want to process 250,000 metric tons of recycled and waste-based raw materials in our production instead of fossil resources as early as 2025,” says Schaffrannek, explaining the objectives – which are also part of BASF’s commitment in global initiatives such as the Alliance to End Plastic Waste or the Ellen MacArthur Foundation. “We are paying particular attention to the value chain for plastics; after all, plastic waste in the environment has become a symbol of the throwaway society we live in today. We must tackle this global challenge together.”
Thanks to our Verbund concept, the principle of the circular economy and the efficient use of resources have been firmly established at the company for more than 150 years
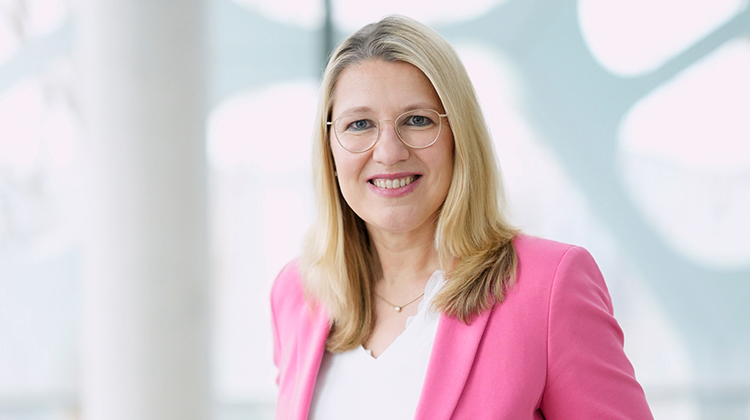
Improved recycling of plastics is part of the solution. “In the discussion about plastic waste, it is often forgotten that plastics offer significant advantages in the production and use phase. They are relatively cheap and resource-efficient to produce, and they have a wide range of uses. For example, they protect foods from spoilage, make cars lighter or insulate houses. Plastics are therefore an important part of the road toward a more sustainable future,” summarizes Schaffrannek. “To unleash the full benefit of plastics, however, we must concentrate even more closely on the end of the product life cycle, where negative effects, such as improper disposal, tarnish the overall picture. We must see plastics for what they are – valuable materials that must be recycled.”
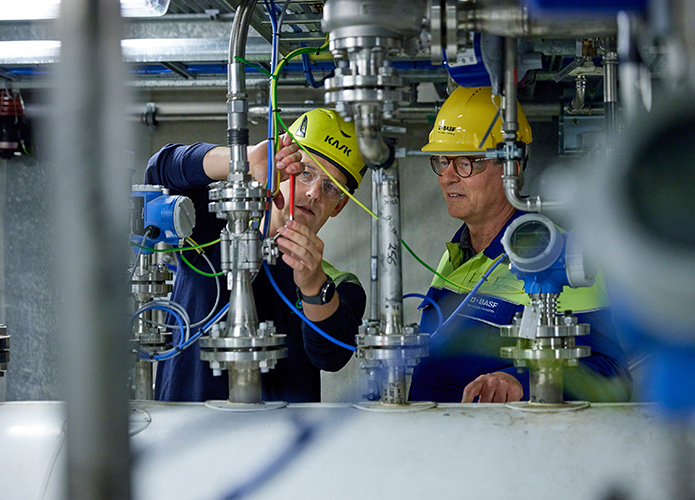
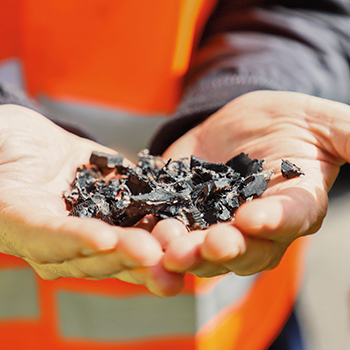
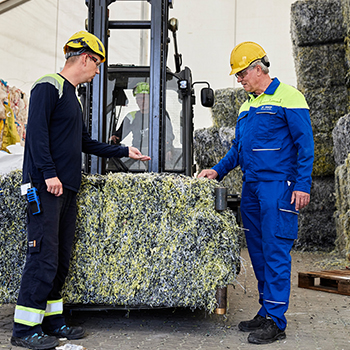
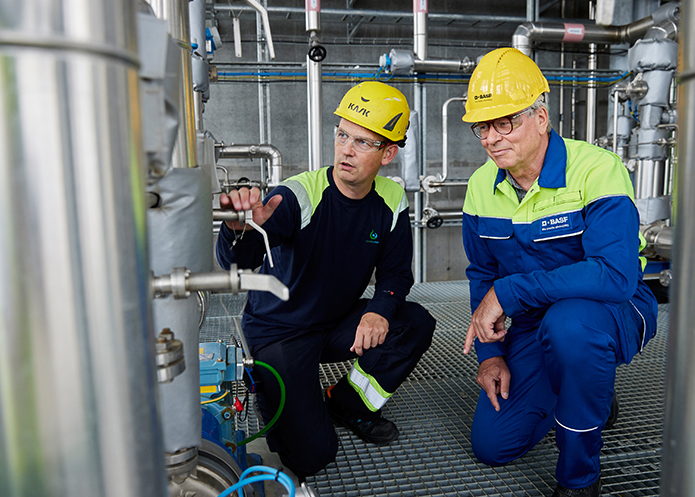
Closing loops thanks to chemical recycling
When viewed from a global perspective, this is still far too rare. Currently, just 20 percent of the approximately 250 million metric tons of plastic waste generated globally every year is recycled. This is partly because there is still a lack of functioning collection and sorting systems in many places. Another reason is that conventional mechanical recycling is not equally suitable for all waste streams, which is why mixed or contaminated plastic waste is nearly always burned or sent to landfill sites. “This is where chemical recycling comes in, as BASF is promoting in the ChemCycling™ project,” says Christoph Gahn, who heads the unit of the same name.
The basic principle of ChemCycling™ is a simple one: In a first step, technology partners break mixed plastic waste and scrap tires down into their basic chemical components. This process is called pyrolysis, and ultimately produces pyrolysis oil. BASF can feed this material into the Verbund instead of fossil fuels and use it to make products with the same quality as new goods. The proportion of recycled materials in the end product is then allocated using a certified mass balance approach. “Chemical recycling is not a replacement for mechanical recycling; rather, it is an additional procedure for waste streams that are not yet recycled using mechanical means for technological, economic or ecological reasons,” explains Gahn.
The mass balance approach
In the chemical industry, the mass balance approach works in the same way as green electricity: The end user does not know whether the exact electricity they use in their own household comes from renewable sources, but as demand increases, the total share of green electricity in the grid also grows. The chemical industry follows the same principle: Recycled or bio-based raw materials are fed into the production processes at the start of the value chains and mathematically assigned to the end products. This calculative allocation offers many advantages: Greenhouse gas emissions are reduced and fewer raw materials are needed, while the quality and properties of products remain unchanged. BASF customers can process the products in the same way as those manufactured using conventional methods and neither the formulations nor the plants or processes have to be modified. As such, customers who purchase mass-balanced products can deploy them as usual and benefit from the identical quality. Independent institutes audit the allocation – in other words the mathematical assignment of the sustainable raw material in relation to the end product.
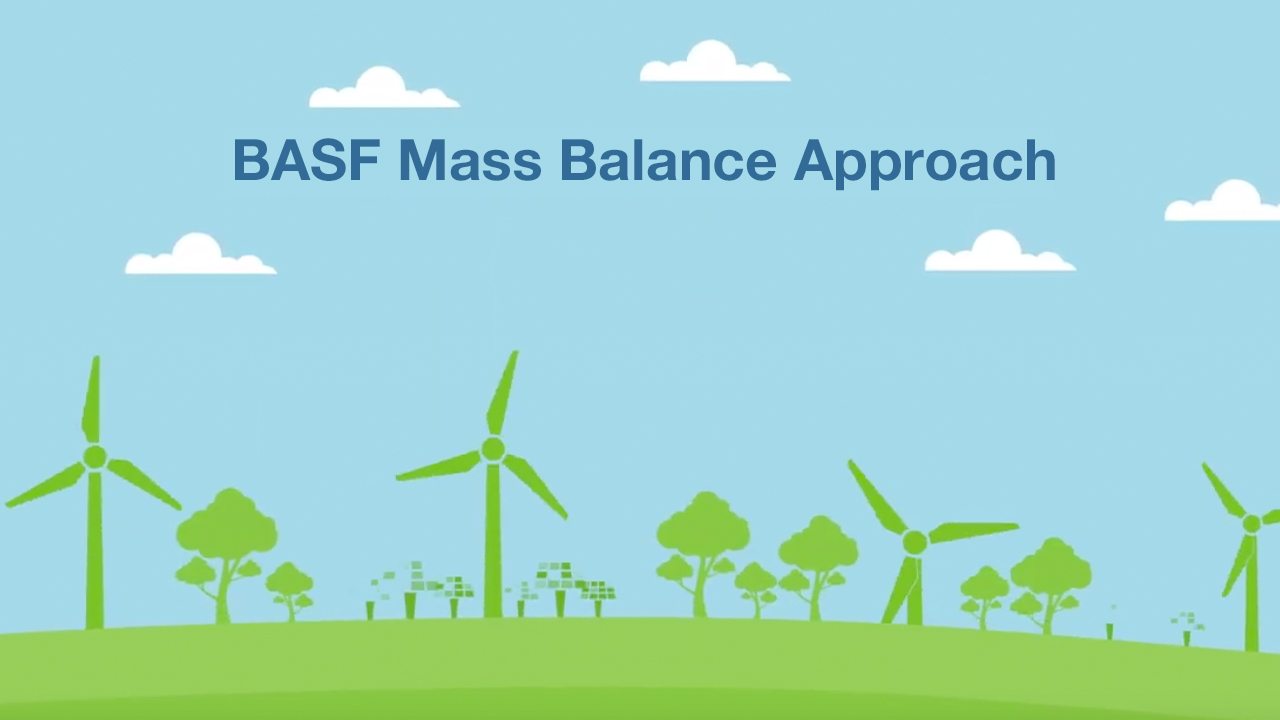
BASF has been marketing products based on chemically recycled pyrolysis oil since the beginning of 2020. The portfolio now comprises around 50 products, which BASF customers use to manufacture transport boxes for sensitive goods such as vaccines or fish, deploy in automotive construction or process in functional textiles, alongside a host of other applications. “We aim to continuously expand the portfolio of CcycledTM products in the coming years,” states Gahn. In order to continuously improve the supply of pyrolysis oil necessary for this and reach the milestone of 250,000 metric tons of recycled and waste-based raw materials, BASF is working closely with numerous partners along the value chain. These include Quantafuel, New Energy and Pyrum, which specialize in manufacturing pyrolysis oil. The ambitious joint objective is to advance and scale the technology so that more recyclable materials can be kept in the loop in the future.
Further improving the mechanical recycling of plastics
Many teams from the Plastic Additives unit of BASF’s Performance Chemicals operating division are also working toward this goal. They focus on solutions for enhancing plastics recovered by mechanical recycling, so that they can then be used in products of the same or even higher quality. “Mechanical recycling has improved considerably over the last few years, as it only leaves a very small carbon footprint. The key challenges are contamination and low polymer quality, which can currently restrict the reuse of these materials,” explains Volker Bach, head of the Global Competence Center Plastics Additives at BASF.
Innovations from the chemical industry can help compensate for these negative side effects of mechanical recycling – for example, the IrgaCycle™ plastic additives launched by BASF in 2021. These help resolve the quality issues of recyclates, including limited processability, reduced long-term thermal stability and insufficient protection from outdoor weathering – even when the share of recyclate in the end product is increased. Moreover, stabilizers help ensure that plastics can be recycled not just once but numerous times.
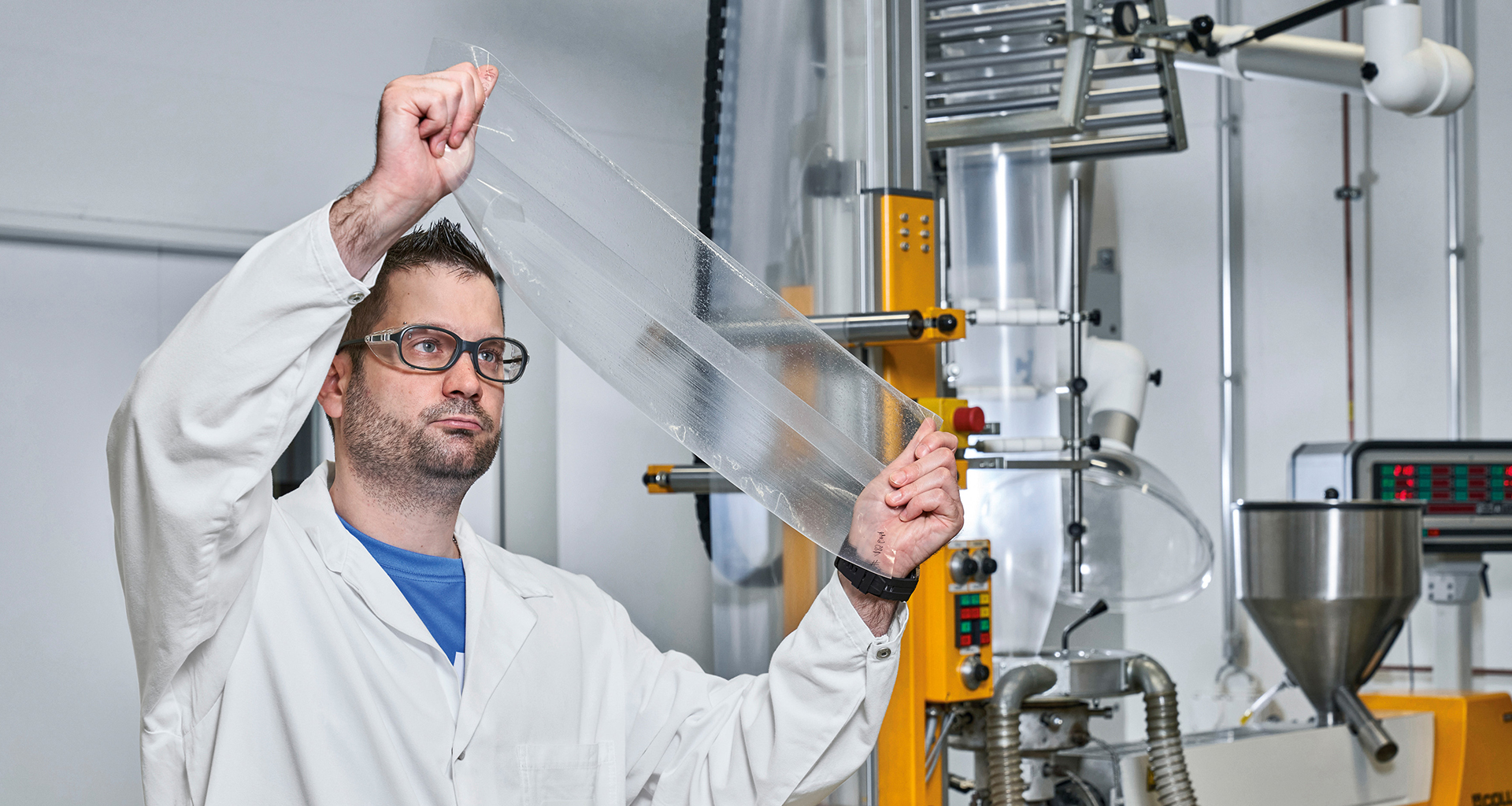
“BASF teams are currently working on a total of more than 35 promising initiatives aimed at developing new raw material paths, material cycles and business models,” says Schaffrannek. These range from innovative methods for the chemical recycling of mattresses and compostable plastics, all the way up to new technologies such as mobile near-infrared spectroscopy or digital watermarking. The latter are used to improve sorting and tracking of various types of plastic. “Innovation is undoubtedly the key to success on the path to a circular future,” comments Schaffrannek. But many other factors also come into play: “Only when all actors in society fundamentally question their patterns of thinking and behavior will new possibilities for a sustainable value creation open up.”
Circular economy: the renaissance of a proven concept
The concept of the circular economy is as old as the Earth itself. Indeed, nearly all natural material cycles and ecosystems work according to the principle of continuous self-renewal. Agricultural societies geared towards self-sufficiency lived in harmony with nature in this manner for many thousands of years. The economic system only changed fundamentally with the advent of the Industrial Revolution – with many positive effects, but also negative consequences such as pollution, climate change and the exhaustion of finite resources. As a result, the concept of the circular economy has been moving into the limelight again since the 1960s – first in science and academia, and subsequently ever more in the economy, society and politics, too. Today, many companies, municipalities, states and associations of states have integrated the concept of the circular economy in their development strategies. The European Commission, for instance, sees the model of the circular economy as an important pillar of sustainable growth in its European Green Deal.